Online Moisture and Temperature Measurement for Solids
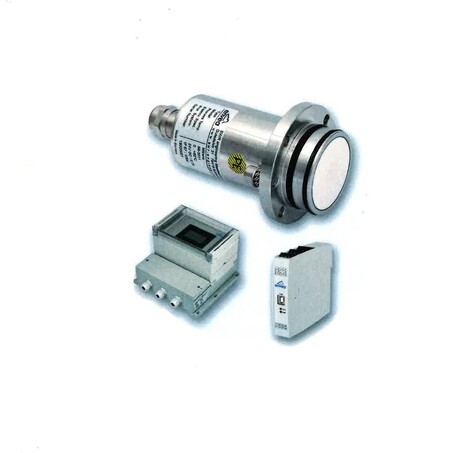
ENVEA (SWR) M-SENS-3 was designed especially for continuous moisture and temperature measurements of bulk solids like powders, granulates and grains for the food processing industry. This microwave technology sensor is also designed to indicate material flow, which allows you to be sure that measured material is effectively flowing in your process. This increases the validity of the moisture measurement and allows you to quickly detect process failure, such as a defective screw conveyor, clogging, etc, via an alarm.
M-SENS-3 is characterised by its uncomplicated installation as well as by its simple calibration. Due to its hygro-stability and its resistance to mechanical shocks and abrasion, the entire sensor is very fail-safe and allows a long service life. The sensor window is protected by a ceramic disc, being very resilient with regard to abrasion and pressure.
This product has been developed to incorporate the latest improvements and advantages in technology, including:
- Online instant and accurate moisture measurement.
- Online process/material temperature measurement.
- With flow detection.
- High temperature and hazardous area versions.
- Maintenance-free.
The calibration is simply carried out by the operator pressing the relevant button on the control unit, then entering the referenced moisture contents. In this context it is convenient that measured value fluctuations by bulk density variations are balanced by an internal filter function. Additionally measured value fluctuations by temperature variations are compensated automatically by the sensor.
A complete measurement system consists of the following components:
- Weld-on sensor mounting flange.
- 1 to 3 sensors, each with a 2 metre connection cable.
- An indicating transmitter in a field mounted housing, or a DIN-Rail format unit.
- Optional Junction Box for connection between sensor(s) and transmitter.
Due to the ability to use up to three M-SENS-3 sensors for an application, connected to a single transmitter, induced measurement inaccuracies, caused by the materials inhomogeneity, can be reduced. At the same time there is reduction of the influence of bulk density variations which normally exist over the whole measurement zone.
Some application examples:
The installation of a moisture sensor in screw feeders proved to be very advantageous, since the material passes by the sensor window in even intervals and with relatively constant bulk density.
By means of the online moisture measurement of solids on a conveyor belt, the operator can react in due time if the material is too humid or too dry. Consequently plugging of subsequent aggregates can be prevented.
Another installation alternative is to mount a sensor at a bin outlet. Due to constant bulk density in case of a filled bin, the sensor finds an almost unchanging measuring field for monitoring the residual moisture. Therefore the M-SENS-3 avoids that too damp material reaches the next production level or arrives into the loading.
After the material lying on the belt has passed through the dryer tunnel, it gets withdrawn from the hot air zone. At the end of the belt the dried material falls in a screw conveyer which transports it to the processing. The operator queries the following points:
Has the material really reached the desired residual moisture value? That is has he chosen the right cycle time and temperature? M-SENS-3 provides accurate and reliable online moisture and temperature values for the process control, by which constant moisture in close tolerances of the output material can be met. This process optimisation enables the operator to manage high savings and quality improvements.
M-SENS-3 can be installed even later on in all types of mixers. The measuring values logging is done within the moving material during the mixer procedure. With the measured moisture value of the material in the dryer process, parameters like detention time and dosage quantity can be controlled.
For this purpose M-SENS-3 is connected to a PLC or another process control system.
For more information, click here.
One Shot Loading: The untapped end-of-line opportunity
As industry focus shifts toward factory-to-freight optimisation, many manufacturers are asking:...
Enhancing product safety and quality control with METTLER TOLEDO's inspection solutions
In the world of food manufacturing, ensuring the safety and quality of every product that reaches...
Heat and Control expands thermal range with Tek-Dry acquisition
Earlier this year, Heat and Control announced the acquisition of UK-based company Tek-Dry Systems...