Considerations for detecting needles and wire in food products for better food safety
By Michelle Schultz, Application Specialist, Thermo Scientific Product Inspection
Wednesday, 08 May, 2019
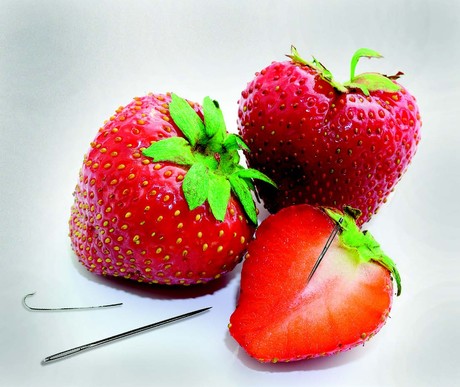
Importance of Food Safety
There are many threats to the world food supply — and once adulteration is suspected or known, global exports and the supply chain to end users can come to a halt. This was evident in the recent tampering of fresh produce with needles.
Foreign object detection in such adulteration events remains a challenge. Ensuring produce is free from small foreign objects requires several considerations:
- Physical characteristics of foreign object
- Cause of entry of contaminant
- Location of the foreign object in the inspected product.
All three have implications for ensuring that foreign objects are detected and eliminated in the supply chain before reaching the end user.
Metal detection and/or X-ray inspection are the two of the most common technologies used to find foreign objects in food. Each technology should be considered independently and based upon the specific application. Following are some key considerations.
Particular challenges with detection of metal slivers, needles and wire
Metal slivers, needles and wires — such as those found in the recent contamination events — are challenging to find with conventional inspection practices because of their variable size, thin shape, material composition, numerous possible orientations in a package and their light density.
How can I best protect against and eliminate foreign materials from my fresh produce?
National food safety guidelines (such as FSANZ, FDA) provide guidance in preparing the most robust solution for a particular environment. It’s the quality team’s job to then consider the type of inspection system to use, either metal detection or X-ray inspection, based on the types of foreign materials possible to enter the process.
Common strengths and weaknesses of metal detection
Metal detection is based on disruption of an electromagnetic field at a specific frequency within a stainless steel case. Any interference or imbalance in the signal is detected as a metal contaminant. Most food products have their own response to this field which must be adjusted, to prevent false positive. Hot, wet, conductive products have more inherent signal than dry non-conductive products which impact the detection capabilities of the machine.
Factors to consider when evaluating metal detectors:
- Metal types, no single best frequency for detection of a specific metal.
- External environmental noise (Motors, vibration & RF interference) can also spike resulting in false rejects or reduced sensitivity the detector.
- Size of product/aperture of metal detector. The detector head size also impacts detection capability since the further the metal gets from the coils, the more difficult it is to detect small metals.
- Product noise can also have a significant impact on detection of metal. All products and metals have a phase angle which, in some cases, can overlap and conceal the metal from being detected. To address this, food processors could install two detectors at 45° angles from each other or use one multiscan detectors with many frequencies running at a time to decrease the effect of product noise.
Common strengths and weaknesses of X-ray inspection
X-ray inspection is a density based optical detection system, so it can be used to identify metallic and non-metallic contaminants. The X-ray beams are passed through the product and an image is collected on a detector. The average gray level of the product is learned as the standard and any areas that are denser (or darker) would be detected as a foreign material by the system.
Factors to consider when evaluating X-ray inspection:
- Physical characteristic of product: homogeneity, physical size of product. In general, items that float in water are not detectable by X-ray systems, such as wood, hair, insects, most plastics and rubber. Aluminum, thin, flat metal, slivers, needles and wires may not have enough density to be seen through the product when perpendicular to the X-ray beam, creating an orientation effect. In that case the diameter of the metal must be large enough to cover the majority of a diode in order to be detected.
- Physical characteristic of the foreign object: photodiode size, density of the foreign material (denser) in relation to product being inspected.
- Robustness of the software to detect changes in foreign material. Non-homogeneous products cause problems because the sensitivity must be set for the densest portion of the product, not the thinnest area. This often means larger contaminants are detected in these products. In this case it’s important to use as many software filters as possible to find objects based on density, shape and size.
Recommendations
Even with a better understanding of each technology from this discussion, you still may not know which technology to select. Yet either metal detector or X-ray inspection is a prudent investment versus no inspection technology.
- Our recommendation for metal detection is the Thermo Scientific™ Sentinel 5000 metal detector with multiscan technology. This system uses 5 frequencies simultaneously to increase the probability of detecting all metals, including slivers, needles and wire of varying sizes, in different orientation and with different compositions. Typically these systems last 10–20 years depending on the environment.
- The Thermo Scientific NextGuard C330 system is the best solution for X-ray inspection. This is an entry-level system built specifically for retail packages. It is simple to operate, cost effective and will last approximately 5–8 years.
- Another option is bulk inspection of the raw fruit directly from the field using either a metal detector or a Thermo Scientific Xpert B600 X-ray inspection system. Running fresh fruit in a single layer through a smaller metal detector aperture will increase the detection capabilities because the product will be closer to the coils. Inspection with an X-ray system will also be improved because the product will appear more uniform in the image, making detection of foreign materials easier.
Summary
Detection of any foreign materials has challenges. To make the most informed decision, ask that the inspection system manufacturer test your product on their equipment so you know the expected range of outcomes and tradeoffs prior to making a purchase. Food safety and quality are vital to the health of brands and consumers.
Find out more at thermofisher.com.au/productinspection.
One Shot Loading: The untapped end-of-line opportunity
As industry focus shifts toward factory-to-freight optimisation, many manufacturers are asking:...
Enhancing product safety and quality control with METTLER TOLEDO's inspection solutions
In the world of food manufacturing, ensuring the safety and quality of every product that reaches...
Heat and Control expands thermal range with Tek-Dry acquisition
Earlier this year, Heat and Control announced the acquisition of UK-based company Tek-Dry Systems...