Getting a grip on pet food pouches
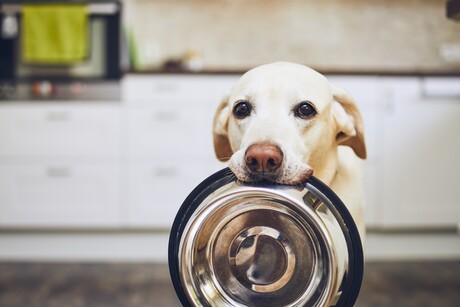
Automated packaging machine builder HMPS recently partnered with SMC Corporation Australia New Zealand to design and custom fit one of its robotic pouch unloader cells with a retrofitted vacuum head for off-loading pouches of pet food from a retort.
Pouches have increased in popularity over the years as a flexible packaging option, and using a vacuum system to handle this packaging option remains a good solution.
“This customer has an old compressor in their factory and requested a solution that is more energy efficient in terms of compressed air,” explained Sergio Palacio, Project Engineer for HMPS.
“Compressors can be expensive to replace; our customer wanted to automate their line without causing unnecessary downtime, additional costs or drastic changes to the rest of the plant.”
Based on the brief from the client, HMPS looked to the modern vacuum technology produced and supplied by SMC to help with the solution.
“We chose SMC’s vacuum products because of their reduced air consumption while offering continuous vacuum where required. We looked to deliver a more efficient and powerful solution with a specially designed and engineered vacuum head,” Palacio said.
Jason Sutton, SMC Area Sales Engineer, said their design departments worked together to deliver an innovative solution. The specially engineered vacuum head used in this application is made up of standard SMC vacuum products — including the ZH vacuum ejectors and ZP vacuum cups — but has been engineered into a unique multifunctional and energy-efficient vacuum design.
“The pouches are wet with traces of chemicals and, as such, we used the ZH series to help take away any water and chemicals whilst protecting the vacuum system,” Sutton said.
“The multi-bellow pads fitted in our vacuum cups (ZP series) are made for quick release and reduced consumption. Because there is no chamber the vacuum response time was immediate, and no air is delivered to a vacuum cup unless it is in use.
“Here, as soon as the air shuts off, atmospheric pressure enters and the multi-bellow pads expand like a spring to assist with the easing of pressure and tension, releasing the product immediately.”
HMPS made use of SMC’s IP65 rated stainless steel products, which are designed to withstand the wet and humid conditions in the factory and meet the health and safety demands. “Components for this application were specifically selected to withstand caustic acid washdowns,” Sutton said.
From SMC’s side, the design for the solution was led by its engineering department in New Zealand, headed up by Sergey Vetrov. “Through the unique combination of a new vision system and SMC’s vacuum head, the customer is enjoying less waste, faster speeds and a reduced cycle time of 15%,” Vetrov explained.
According to Vetrov, this robotic cell can process 576 products per minute and is able to handle four different pouch sizes and four different gravy contents. “It’s important to note that the gravy affects the shape of the product and the performance of the vacuum head. The vacuum cups used for this application adjust to ensure constant suction when required. This same technology can be applied across an array of products in pouches such as soups, rice, biscuits, etc.”
The latest machine for this pet food application is said to perform far better than its predecessor and has achieved 28% in energy savings. As a result of the success, the customer now plans to retrofit the vacuum head on an additional three machines.
Phone: 1800 763 862
Key Technology COMPASS Belt-Fed Optical Sorters
Key Technology introduces the COMPASS belt-fed optical sorters.
Olivo multi-temperature food transport solution
CoolPac has introduced Olivo insulated food containers, which are designed for the transportation...