The smart way to achieve greater plant safety
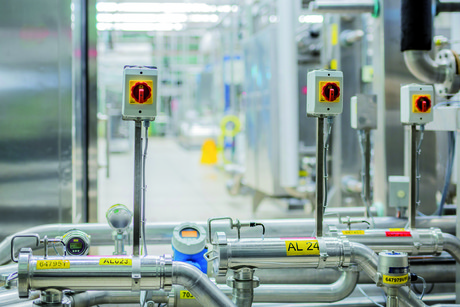
In process technology, automated plants are designed for long-term operation. Safety requirements nonetheless change over time. Today, the minimum requirements placed on machinery and plant safety standards are regulated by Machinery Directive 2006/42/EC. Hence, certain performance levels must be met according to the plant design to ensure adequate protection for the life and health of workers, eg, when carrying out tasks on pipelines, valves, connectors or similar. Danone GmbH was able to simply retrofit the desired safety standards in the existing plant at its production site in Ochsenfurt near Würzburg, Germany — thanks to the new Bürkert valve types that guarantee safe shut-off.
Safety technology upgrade welcome
At its site in Ochsenfurt, Danone GmbH mainly produces yoghurt and desserts for the German market and for export to neighbouring European countries. To meet the new safety requirements for maintenance, repair and cleaning work, changes to the safety concept were required at a plant that had been installed several years ago. The existing safety standards were already very high — emergency stop switches were, for instance, secured by locking mechanisms against accidental reset in the event of a shut-off. Furthermore, certain valves in the extensive pipe system between the 16 tanks and six filling lines could be switched off by the control unit via PROFIBUS. The plant operator nevertheless wanted to enhance the level of safety for its workforce. The aim was to achieve Performance Level C, which is relatively high for this application. Guaranteed safety was very important to the management team, particularly for the performance of cleaning work. Cleaning agents containing acids and bases that heat up to 80°C are used during cleaning processes. If a pipeline section, eg, when cleaning the used sieves, is not reliably shut off or if an electrical or mechanical safety measure is bypassed, members of staff could indeed be severely injured.
The practical alternative
The previous installation consisted of a decentralised peripheral system from Siemens (ET 200S) with integrated pneumatic output modules from Bürkert, which are installed in the vicinity of the process inside stainless steel control cabinets. These Type 8644 valve islands can control electric and pneumatic signals via a bus line. The aim now was to reliably exclude the risk of certain valve functions being activated unintentionally via PROFIBUS due to a control error when workers are carrying out necessary tasks on-site at the pipeline system. Typically, such requirements are resolved using a PROFIsafe controller, the PROFIsafe protocol and respective fail-safe IO modules. This type of retrofitting is, however, expensive due to unwanted downtime and the costly replacement of numerous components. But there was a practical alternative: the respective valve functions can also be shut off safely and directly on the existing valve island — that is on the pneumatic modules at the ET 200S — if the valves here are retrofitted with an additional connection for safe shut-off.
Simple function — great impact
The Type 6524 and Type 6525 pneumatic valves with additional shut-off function can be shut off independent of the regular switch signal control of the valve island. Valve integration is possible at any valve slot on the valve island. The valves consist of a pilot flipper solenoid valve and a pneumatic seat valve. The flipper action system allows the switching of high pressures combined with low power consumption and fast switching times. The patented shut-off function is implemented via a second connection. The valves are still controlled via the bus but additionally offer a second electric connection via which the power circuit of the solenoid coil can be interrupted. When triggering a safety chain, the normally closed contact of an emergency stop relay shuts off the coil of the pneumatic valve, irrespective of valve activation by the PLC.
How users benefit from Bürkert solutions for retrofitting safe shut-off:
- Reliable plant safety: The new pneumatic valves can be shut off independent of the regular switch signal control of the valve island.
- Flexible retrofitting: Integration of the valves is possible at any valve slot on the valve island. Undesired downtime and costly replacement of components are avoided.
- Less space required: Application of pneumatic and electric components in the control cabinet is reduced thanks to the new valves. The size of the control cabinet can thus be smaller than in the past.
Fast-Track Food Safety with 2-Hour Listeria Testing
When Neogen introduced its Molecular Detection Assay at the International Association for Food...
Serving Up Efficiency: Why AI is the Next Big Ingredient in Food Manufacturing
With margins tight and supply chains unpredictable, AI-powered systems are becoming the secret...
Optimized CO2 concentrations in greenhouses translate into higher productivity and higher quality
In greenhouses, the growth rate and development of all plants can be improved by controlling...