The agile food producer
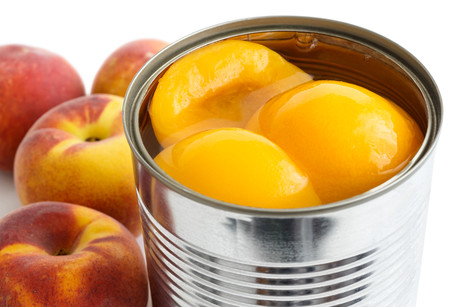
Being a food manufacturer comes with a number of challenges as companies try to meet the growing demands of customers and remain profitable in a largely low-margin industry. This is essentially true no matter where in the world you have production facilities.
Gone are the days when you could produce a small number of products on long-sustained production runs. Instead, you’re producing more products in more varieties — for changing health, taste, image and cost preferences — in a greater range of packaging options. You’re also fighting to balance the demands associated with branded products versus private label to maintain a foothold in existing markets, which are becoming increasingly segmented, while competing against global and local food manufacturers in emerging markets, such as China, India and Latin America.
Amid these competitive challenges, businesses also must contend with internal and external forces, such as limited capital funding, high commodity prices, legacy facilities and equipment, increasing regulations, and ageing workforces.
It’s more important than ever to be prepared to do more with less. That means understanding the entire manufacturing spectrum and identifying areas where improved efficiencies can be realised. Food companies need to place greater emphasis on achieving operational improvements, increasing asset utilisation, maximising yield, increasing throughput and improving safety.
Proactively seeking improved efficiencies and then taking real action to achieve them will better position you in this highly dynamic, continually evolving industry to retain your hold in different markets and stay in the black.
More products — and more product varieties — are being made than ever before. According to the US Department of Agriculture (USDA) Economic Research Service, the number of new food and beverage products introduced in the United States alone grew from less than 10,000 in 1992 to more than 21,500 in 2010. Additionally, a 2012 KPMG survey said that new products and services would be the top focus for food manufacturers’ capital spending for the following year.
Concurrently, long-time sought-after brands from the West have seen their dominance dwindle in emerging global markets, where regional products and private labels have increasingly won the favor of the growing middle classes.
This presents many challenges — increasing commodity prices, ageing equipment and infrastructure, more stringent yield expectations, higher shipping costs, global competition — for businesses that are largely unseen to customers, who merely want their preferred brands to be available, consistent in quality and at the price they’re accustomed to. And with more food options available to them than ever — whether from local niche providers or big-box national retailers — these customers have more reasons to leave their brands for something new, better or cheaper.
Summary
The food-production process too often takes place in a black hole, with a lot of unknowns on the plant floor — from the real value that assets provide to the ‘how’ and ‘why’ behind line failures.
Limited capital funding may mean the ideal ‘100% efficient’ operation is unattainable. But working with automation- and safety-solutions providers can equip you with a better understanding of your production cycles and discover where efficiency improvements can be achieved that translate into real cost savings.
Rockwell Automation works closely with companies to deliver validation and value statements before investments are made, allowing you to see potential for improvement — improving yield by X percent, reducing maintenance time by Y percent, increasing line throughput by Z percent — and the estimated dollar value of those investments.
As the food market gets bigger and your operations get leaner, the key to success will be finding efficiencies that drive success across your entire production process.
Full Article URL: https://literature.rockwellautomation.com/idc/groups/literature/documents/wp/food-wp005_-en-e.pdf.
Fast-Track Food Safety with 2-Hour Listeria Testing
When Neogen introduced its Molecular Detection Assay at the International Association for Food...
Serving Up Efficiency: Why AI is the Next Big Ingredient in Food Manufacturing
With margins tight and supply chains unpredictable, AI-powered systems are becoming the secret...
Optimized CO2 concentrations in greenhouses translate into higher productivity and higher quality
In greenhouses, the growth rate and development of all plants can be improved by controlling...