Improve food product safety with detectable elastomers
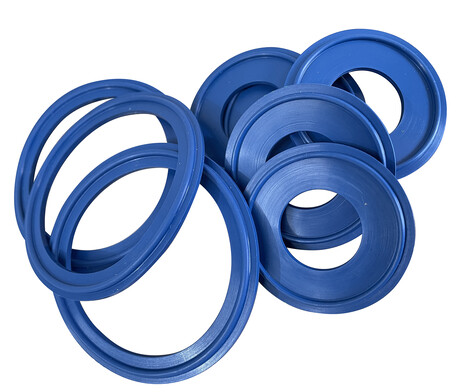
Product inspection has become an indispensable part of responsible food production and an absolute prerequisite for successful food safety certification. Any contamination of food with impurities of any kind may have serious consequences for a company, because under the product liability laws every food producer is liable for contamination of product in the case of a consumer being harmed.
Over time and with repeated clean-in-place, sterilisation, and handling during equipment cleaning, component parts used in food and beverage processing equipment and pipework can degrade. As a result, contamination can occur due to small metallic and non-metallic contaminants being deposited into the product.
Of the various automated inspection systems in use, metal detectors and x-ray technologies are commonly used to detect this type of contamination. But not all contaminant materials, such as elastomers, are detectable using these technologies.
The dangers of elastomer contamination
As a result of excessive use, shearing and damage can occur to gaskets, causing undetectable product contamination. When rubber breaks off a moving part it can migrate through the processing system and into the product. Searching for and locating fragmented rubber parts is a costly, time consuming and an inconclusive process.
Not locating a worn and lost rubber piece can have an even costlier outcome.
In the past, companies didn’t know there was a problem until an end-user discovered elastomer particles in their food. When an elastomer breaks off into product and isn’t discovered immediately, losses include more than the price of wasted goods: containing, reinspecting, or disposing the contaminated product can incur expensive costs and inflict damage on a brand’s reputation.
Detectable elastomers
To overcome the issue of undetectable elastomer contamination, FOX Global — an importer, manufacturer and distributor of hose, valves fittings and industrial solutions for the food and beverage industry — now offers a line of metal detectable and x-ray inspectable seals and gaskets. Utilising a standard elastomer with a metal-impregnated compound means that displaced rubber material can now be located by a metal detector.
These components make it possible to detect any part of the gasket or seal that has sheared off because the metal particles infused in the material allow metal detectors or x-ray equipment to easily locate the material in fluids or other material.
The range of metal-detectable components include:
- Tri-clover seals
- Camlock gaskets
- Flange gaskets
- O-rings
- Sheet material
- Custom gaskets
Designed to work with existing stainless-steel piping and hose systems, the Rubber Fab line of products can be spotted by in-line x-ray inspection and metal detection systems as well as magnetic separators.
As the world’s largest provider of elastomer products, Rubber Fab is the only company that has been able to find the right formula for this type of elastomer. The company patented the design and named the product family Detectomer.
Detectomer fragments can easily be detected allowing automated systems to reject contaminated product, and allowing worn parts to be replaced without great expense or costly downtime.
Broad range to suit most applications
FOX Global’s growing Rubber Fab range offers FDA and 3-A certified products, enabling manufacturers and end users to select the appropriate product to meet the temperature, chemical and specific performance needs.
The Detectomer range of products can be x-ray detected in use with packaging and product that includes glass, metal, stone and high-density plastics, even for products packaged in foil or metalised film. The range is also designed for demanding steam applications, high temperature and hot oil applications.
Being able to easily detect lost elastomeric fragments reduces production downtime and can reduce product loss while preventing the distribution of contaminated product and the resulting product recalls.
Fast-Track Food Safety with 2-Hour Listeria Testing
When Neogen introduced its Molecular Detection Assay at the International Association for Food...
Serving Up Efficiency: Why AI is the Next Big Ingredient in Food Manufacturing
With margins tight and supply chains unpredictable, AI-powered systems are becoming the secret...
Optimized CO2 concentrations in greenhouses translate into higher productivity and higher quality
In greenhouses, the growth rate and development of all plants can be improved by controlling...