How digital capabilities are transforming the way we work
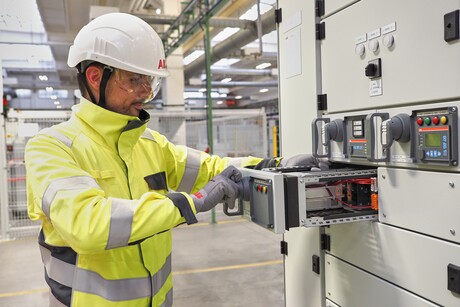
Electrical systems in industry have, until recently, been managed in a rather traditional way, with regular, routine maintenance activities being carried out to prevent switchgear from becoming unsafe or breaking down. But with customers increasingly looking for improved productivity, continuous operations and high reliability — not only in heavy industries but in light ones too — the way we service these electrical systems is evolving at pace.
ABB NeoGear low-voltage switchgear technology has paved the way for a smarter future, with next-generation safety inbuilt by design and minimum risk of failure and reduced need for maintenance.
As the operator of a plant, for example, the more information you have about its electrical systems the better, so that you can understand when and where maintenance may be required or when equipment should be replaced. You are also in a better position to plan the production process and to, ideally, move from a typical 1- to 2-year maintenance cycle to a far longer one.
Digital capabilities help operators plan more effectively, to ensure continuous, long-term productivity. The idea behind ABB’s digital switchgear solutions is not only to measure and monitor conditions more closely, but to provide our customers with technology that takes care of itself, freeing them up to focus on other areas of their business.
The benefits of digital capabilities
Temperature monitoring is just one of the processes that has been made easier by the advent of digital switchgear. The temperature change of an electrical connection is always the first and best indication of the existence of bad joints. In traditional environments, operators need to have maintenance teams available up to three times a year to safely enter the switchgear room and measure the temperature of accessible joints.
However, with digital switchgear this exercise becomes redundant, thanks to integrated sensors that monitor the temperature 24/7, as well as fluctuations in other conditions such as load changes, without the need for human verification. Not only does this enable a clear and ongoing understanding of any abnormal activity, it also ensures operators only intervene when necessary and, if they must enter the environment, it informs them what safety wear is necessary. Ultimately, the process is less disruptive, more cost-effective and safer.
Beyond this, operators can monitor the mechanical and electrical condition of devices in the switchgear, such as circuit breakers. Information is also collected about the environmental conditions where the switchgear is operating, which can impact the lifetime of components.
ABB NeoGear revolutionising energy distribution:
- No exposure to live parts
- Reduces the physical switchgear footprint by up to 25%
- Increases cooling efficiency to reduce heat losses by up to 20%
- Reduces overall operational costs by up to 30% through predictive maintenance, increasing uptime and performance
- 30 unique parts vs up to 400 in traditional busbar
- 90% fewer electrical joints for highest switchgear availability
- Arc ignition protected zones keep maintenance personnel safe
Industry 4.0
To make technology even more intelligent, the challenge today is, firstly, being able to collect enough data over a long enough period, and, secondly, having the right tools in place to effectively analyse it, both automatically and continuously. That’s why our next step is to look at Artificial Intelligence and Machine Learning algorithms, to help us to better understand the data being collected, so that we can turn it into actionable insight for industry — optimising processes, improving safety and making better business decisions.
Workers — some of whom have been working in their industry for 20–30 years — are currently in a transition period when it comes to digitalisation. We want them to see these technology advancements as an advantage — and a great opportunity. With smart solutions that work intuitively, workers can maximise their time and spend more of it doing valuable, meaningful work.
Just as new digital technologies are coming into the marketplace, the electrical engineers coming into the workforce today are digital natives. As such, they want to be able to access the information needed to do their jobs on their smartphone or tablet — as they would in other areas of their life. They expect to be guided by the technology, prompting them as to when and where they need to carry out maintenance work and the steps necessary to carry out that work.
This technology is already a reality, and many of our customers reap the benefits of the ABB Ability™ Condition Monitoring for electrical systems (CMES), installed as an integral part of the switchgear assembly. The CMES allows switchgear operators and plant maintenance engineers to monitor and manage electrical distribution systems and the motor control center via their mobile devices, in real-time, to optimise maintenance, operational costs and energy consumption.
Tomorrow’s world
Digital natives expect instant access to everything they need in one place, such as safety checklists and condition reports. Tablets and other mobile devices, combined with augmented reality, where workers wear smart glasses that display the information they need right in front of their eyes, is what the future looks like for engineers. The days of following paper instruction manuals to make repairs are most definitely numbered.
To stay one step ahead of workers’ (and customers’) expectations, manufacturers and businesses must continue to push the boundaries, using digital technologies to create smarter, more intuitive ways of working. Five years ago, nobody thought it possible that we could create a digital switchgear like ABB’s NeoGear. But now that it is here, it has changed the way we work with and maintain this vital electric power component.
Download this whitepaper to learn more about NeoGear and its application.
Fast-Track Food Safety with 2-Hour Listeria Testing
When Neogen introduced its Molecular Detection Assay at the International Association for Food...
Serving Up Efficiency: Why AI is the Next Big Ingredient in Food Manufacturing
With margins tight and supply chains unpredictable, AI-powered systems are becoming the secret...
Optimized CO2 concentrations in greenhouses translate into higher productivity and higher quality
In greenhouses, the growth rate and development of all plants can be improved by controlling...