Have you got the right technologies for your food processing applications?
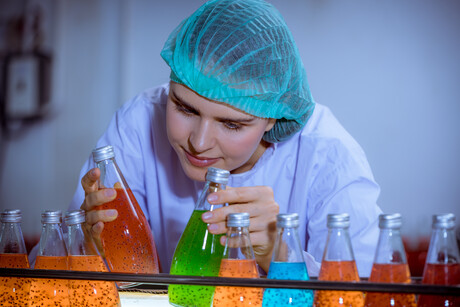
The food we eat might not know where it comes from or which processes it passes through but we expect it to be safely available and of good quality!
Food has travelled around the globe since ancient times but as production technology and transport methods evolve, the volume has increased significantly. If the right technology is not used in food processing or manufacturing then it could cost five times as much to recall a product as it does to distribute it, even before other costs such as legal claims, product disposal, loss of brand reputation and loss of market share are ruminated. A sure way to attain peace of mind and avoid these costs is by identifying the right technology to implement from the beginning.
The food industry works hard to ensure safety, with fundamental programs of pest control, basic hygiene, employee training, good laboratory practices, hazard analysis and critical control points (HACCP) programs, foreign matter controls, and the lists go on... The thing to remember about food safety is that it is not a competitive advantage, it’s a point of entry. Having the right technology in food processing or manufacturing plants is crucial in order to avoid contaminants.
Compressed air in food processing
Compressed air is used in a broad range of applications in the food processing industries such as mixing of ingredients, cuttings, spraying, drying of product, transporting/propelling product through processing systems and packaging of final product. In many of these applications, compressed air is in direct or indirect contact with food product. If the correct technology is not selected or not treated correctly, impurities in the compressed air may contaminate the food product which can result in change in colour and taste, reduced shelf life. In addition, exposure to bacteria and other microorganisms can result in product recalls.
On-site generation of product gases such as nitrogen and carbon dioxide, and its usage for food safety or preservation and carbonated products respectively, are equally imperative within the food industry.
Equipment or technology selections for compressed air and product gases handling needs attention with regards to products and or processes where contaminants are concerned.
End-to-end solutions for every food and beverage production process
Atlas Copco have been supporting many food processing plants in Australia for process air, plant air, packaging or other applications. We have the compressed air solutions that you need. We have all the in-house technologies for every step of the production process meaning we can offer an efficient one-stop solution for your compressed air needs.
Clean air for the highest industry standards
Atlas Copco has set the standard for contamination-free compressed air in the food and beverage industry. You can rely on the largest range of oil-free technologies within the industry, knowing that you work with the first compressor manufacturer to achieve ISO 8573-1 (2010) Class 0 clean air, certified by TÜV Rheinland. Air compressed for food and beverage production by our compressors is of the highest grade of purity to reduce any possibility of contamination and to protect your hard-won reputation.
Reliability and efficiency
When we say we have the lowest total cost of ownership possible, we mean it. Maximise your production process’ uptime thanks to our globally installed service network that expands over 180 countries, combined with monitoring systems such as the Variable Speed Drive and SMARTlink that allows you to carefully plan any needed maintenance, thus decreasing the span of possible downtimes.
What's new in food processing applications solutions from Atlas Copco?
Nitrogen
Nitrogen is used in various food & beverage processing and packing applications for preservation and food safety. Atlas Copco on-site nitrogen generation can be combined with existing compressed air set-up or if you’re thinking of putting in a brand-new plant, then nitrogen generation can be integrated along with your compressed air needs. Atlas Copco on-site nitrogen generation to your doorsteps provides huge benefits, not only operating cost reduction but also on-demand supply, independence of third parties, peace-of-mind and increased production uptime, from meeting erratic demand fluctuations and nitrogen generation to required nitrogen pressure and purity right up to 99.999%.
Explore more about Produce Your Own Nitrogen On-site using Atlas Copco Nitrogen NGP+ PSA technology principle... NGP+ installation animation.
Carbon Dioxide
Carbon Dioxide is widely used in many food & beverage processes — for example in breweries, carbon dioxide is generated as part of the fermentation process and used in the brewery final process, including all carbonated drinks.
Carbon dioxide is a major greenhouse gas (GHG) and there is strong evidence that GHGs are one of the primary causes of the global warming. From carbon dioxide recovery or generation from your processes, Atlas Copco Carbon Dioxide drying and oil-free compression (boosting) safeguards the compressed carbon dioxide quality for end product use, which not only results in operating cost reduction but also on-demand supply, independence of third parties, peace-of-mind, and increased production uptime, and most importantly CO2 – ZERO declaration -> Green process certification for customer end product.
Refer to the video: SP Italy uses CO2 to control insect pests in their production process to guarantee rice quality and safety. At the end of the process, instead of being released in the atmosphere, the CO2 is recovered up to 80%.
How do you know you’re choosing the right technology company to partner with?
The first step is to be very clear about the strategic competencies you need and your requirements for the project or process. Going with the lowest price is often not the best decision. Before you solicit a technology partner, make sure your vision, budget and timeline are realistic and most importantly are the real process requirements within the food industry!
Here are some crucial question areas to help you evaluate and choose the right technology partner for your compressed air and produce gas requirements needs:
How do you find potential technology partners?
- Ask for referrals from trusted contacts and be sure you understand why they recommend the vendor.
- As you consider candidates, examine vendor areas of strength, depth of experience, and client portfolio, technologies, ask for customer references and past performance summaries for similar projects to yours.
- Consider how established, experienced and stable the vendor is (i.e. years in business, financial stability, recognition and awards).
- Make sure a vendor provides the full gamut of services you will need, such as specialised subject matter expertise, support and training.
- Most importantly to understand — Is this technology aligned to my/our company’s business objectives?
- How great is the presale process? If you are not impressed with expertise, responsiveness, thoroughness, communication, and enthusiasm, it’s unlikely things will get better. Consider the quality of the people you’re partnering with, rather than just the costs that can be saved.
- Will you be able to be face-to-face when it really counts? Project kickoff, gathering requirements, design stage, equipment selections and milestone releases are key phases where communication and collaboration needs to be highly effective. Communication is key to any successful client/supplier relationship, but food industry technology projects demand a greater degree of skills to ensure the thousands of details and different stakeholder requirements are understood and integrated correctly into the process.
- Will the vendor transfer knowledge to your team? Vendors often have you rely on them for basic system/process maintenance, which can be an unexpectedly high post-deployment cost. Think about lowering these costs by training your internal staff to handle this and discuss the option with vendors. Make sure this is addressed fully and favourably for your needs in the proposal.
Choosing a technology partner always entails some degree of risk. You can dramatically increase your chances of success by asking the right questions and be much more confident in your decision by thoroughly understanding the processes and technology used by your prospective partner.
Take advantage of what great partners can really offer — new strategic competencies. Whether you need strategic direction to help you innovate and compete, with the right partner, you can leverage the best and right technology available and instantly gain the capabilities for success, which can be capitalised and marketed.
Enhancing product safety and quality control with METTLER TOLEDO's inspection solutions
In the world of food manufacturing, ensuring the safety and quality of every product that reaches...
OD200: New Compact Distance Sensor Raising the Bar in Performance and Reliability
Launching in June 2025 from SICK’s HQ in Waldkirch, the new OD200 miniature distance sensor...
Heat and Control expands thermal range with Tek-Dry acquisition
Earlier this year, Heat and Control announced the acquisition of UK-based company Tek-Dry Systems...