Flow meter helps sugar mill improve plant efficiency and handle a varying steam demand
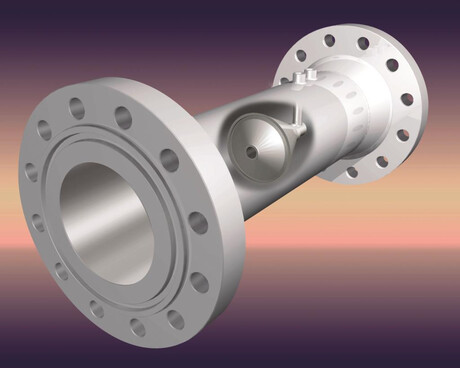
With demand for sugar products growing worldwide, production is rising at many mills including one in Latin America that relies on steam heat as part of its process that converts raw sugar cane into molasses, sugar and related products. The mill’s production team was tasked with transferring excess steam from its production system to a nearby bio-ethanol plant operated by the same parent company.
A typical sugar mill first extracts raw sugar from the cane, and then processes it further for a variety of consumer and commercial uses. The mill cleans, cuts, chops and shreds the cane and then adds water before heavy rollers crush out the sucrose juice. The liquid is then mixed with other substances prior to further refinement in several complex steps that eventually create granulated sugar or other products.
The left-over pulverised sugar cane material is burned to fuel the mill’s process steam boilers, which send steam to large turbines that create co-generation electric power.
Problem
In this application, the sugar mill’s high-pressure operating environment was a cause for concern with some flow sensing technologies creating problems with physical plant efficiency. Those technologies that rely on moving turbines or plates can be problematic in high-pressure (steam) applications. They can even pose a serious safety hazard if a piece should break off during operation and pass through the line into other equipment.
Process control and demand had also grown over time to be a real challenge. Variable line pressures occur when the steam flow is irregular due to seasonal high/low climate temperatures or changes in steam production relating to a drop or increase in feedstock. The result can be depressurisation or a pressure spike that causes stress to the mechanical parts. These types of conditions eventually require costly maintenance and recalibration with some flow sensing technologies.
Solution
After the process engineers at the sugar mill reviewed many flow sensor technologies, they contacted the flow measurement applications team at McCrometer. The team at McCrometer quickly recognised the harsh operating environment and low-maintenance requirements, which led them to suggest the V-Cone® flow meter for this application. This recommendation proved to be a great improvement to the sugar mill’s physical plant efficiency as well as providing a solution to the process demand and control issues the plant was experiencing.
The V-Cone flow meter developed by McCrometer could provide precision steam flow measurement for the sugar mill and simultaneously require no maintenance in this demanding process where high pressure conditions exist. Sugar mill plant safety was also immediately improved due to the V-Cone flow meter’s unique design boasting no moving parts. There was no danger of anything breaking off and causing safety issues down the line or into other equipment.
Additionally, the V-Cone flow meter’s smaller footprint required up to 70% less straight pipe without being affected by flow disturbing equipment up or down stream. Its self-conditioning design allowed the sugar mill process team to place the flow meter exactly where it was needed without the costly addition of extra pipe, external flow conditioners or complicated space-consuming layouts.
The rugged, no moving parts V-Cone flow meter could measure clean, abrasive, dirty, and particle laden fluids over a wide range of Reynolds numbers without wear or clogging concerns, resulting in an unprecedented 25-year operating life with no need for maintenance (Reynolds numbers are a measure of whether flow is laminar or turbulent.)
Shear stress occurs in laminar and unstable turbulent flows. The V-Cone flow meter’s very stable turbulent flow all but eliminated the stress and consequently resulted in no surface deterioration. Additionally, due to the shape of the cone, there was little chance of cavitation on the backside of the cone to erode the surface. Additionally, V-Cones do not need regular maintenance or recalibration after installation, which greatly appealed to the sugar mill’s desire to improve plant efficiency.
Result
The first V-Cone flow meter for the sugar mill was installed in a sixteen-inch line and has been operating successfully since 2005. The owners of the sugar mill plant expanded the distillery plant where they have the same application for a larger thirty-inch line. Since the plant found the original V-Cone flow meter reliable, repeatable, and accurate with no need for recalibration or adjustments for maximum uptime, purchasing a new thirty-inch V-Cone was an easy choice. The sugar mill is pleased to report improved process control and demand, as well as greater physical plant efficiency since making the change to V-Cone.
Fast-Track Food Safety with 2-Hour Listeria Testing
When Neogen introduced its Molecular Detection Assay at the International Association for Food...
Serving Up Efficiency: Why AI is the Next Big Ingredient in Food Manufacturing
With margins tight and supply chains unpredictable, AI-powered systems are becoming the secret...
Optimized CO2 concentrations in greenhouses translate into higher productivity and higher quality
In greenhouses, the growth rate and development of all plants can be improved by controlling...