Enhancing Compressed Air Systems Efficiency with Process Instrumentation
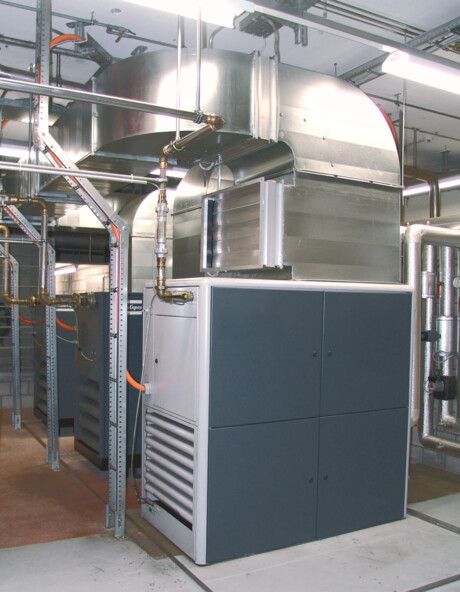
Compressed air systems are essential to many industrial processes in the food & beverage industry. As such, it’s one of the main contributors to your sky-rocketing energy bills as it can negatively impact your production regarding availability and maintenance if not produced and distributed correctly.
Relax, there's a way to tame this beast!
According to the Australian Department of Climate Change, Energy, the Environment and Water, metering and monitoring your network is a quick win in terms of energy savings[1].
Let's elaborate.
By monitoring critical components of compressed air systems, such as flow and pressure, it's possible not only to reduce energy costs but also to improve delivery performance and quickly identify leaks and anomalies in your network.
A practical example is measuring the energy consumption of your compressors with the amount of air generated. This gives you a clear idea of the costs associated with production and sets the benchmark to evaluate if reduction initiatives are effective and support your ROI calculation.
In addition to monitoring the amount of air generated, monitoring the compressed air flow across your network allows you to identify your main consumer areas and understand production patterns (i.e. periods of high and low demand).
This is a powerful resource to identify leaks in the distribution system.
A simple way to do it is to monitor air consumption during idle/low-consumption periods and check if the consumption is consistent. Suppose it's too high — that is a strong indicator of leaks in the area.
Additionally, by understanding your process consumption dynamics and combining it with real-time data generated by process instrumentation, it's possible to create effective control of multiple compressors, allowing switching off compressors that are not needed and ensuring they are working in their optimal load range.
Let's not forget about the role of pressure monitoring: It is critical to ensure not only the availability and the efficiency of equipment that needs compressed air for its operation, but also to understand if there are significant pressure drops that might be decreasing the efficiency of your system.
Over-pressurised systems will increase energy consumption with non-practical effects on productivity, leading to energy waste and increased losses in case of leaks across the network.
By monitoring the pressure across your compressed air network, it's possible to ensure the minimum pressure necessary for production and identify areas and equipment that need maintenance, such as clogged filters.
More than just giving you a clear picture of the health of your compressed air system, process instrumentation gives you the data and the insights you need to reduce your operational costs while ensuring your plant availability.
Do you want to know how to keep track of the efficiency of your compressed air system?
https://cx.endress.com/LP=4901
Reference
[1] Compressed air - Australian Department of Climate Change, Energy, the Environment and Water https://www.energy.gov.au/business/equipment-and-technology-guides/compressed-air
Enhancing product safety and quality control with METTLER TOLEDO's inspection solutions
In the world of food manufacturing, ensuring the safety and quality of every product that reaches...
OD200: New Compact Distance Sensor Raising the Bar in Performance and Reliability
Launching in June 2025 from SICK’s HQ in Waldkirch, the new OD200 miniature distance sensor...
Heat and Control expands thermal range with Tek-Dry acquisition
Earlier this year, Heat and Control announced the acquisition of UK-based company Tek-Dry Systems...