Dispense Gas Monitoring in the Hospitality Industry
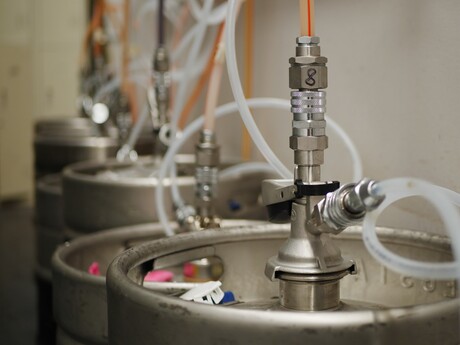
Gas monitoring in areas where beverage dispensers are located is key to mitigating risks associated with carbon dioxide toxicity and oxygen depletion. AS 5034 outlines the OH&S standards to ensure worker safety in non-ventilated areas.
Carbon dioxide is used in the hospitality industry in many applications such as carbonating soft drinks or for beer taps. Cylinders of dispense gas are usually a mixture of carbon dioxide and nitrogen. If the cylinder or any of the gas control equipment leaks, the dispense gas will replace oxygen in the atmosphere and there is a high risk of exposure and/or asphyxiation.
Signs of exposure can range from breathing difficulties and headaches to unconsciousness and death. Ensuring that areas are safe for workers and that anyone, who needs to be in the area, is properly trained should an emergency occur will help prevent injuries or fatalities.
Ventilation & Detection:
AS 5034 covers the installation and use of inert gases for beverage dispensing.
- Scope: This Standard specifies the requirements for the design, location and installation, testing, commissioning, safe use, and maintenance of the compressed inert gas or refrigerated liquid equipment and reticulated and portable systems necessary to dispense beverages.
Often, CO2 cylinders for beverage dispensing are kept in confined spaces with limited ventilation. AS 5034 specifies that all cellars and storage rooms without natural ventilation need gas monitors installed.
Naturally ventilated areas must have one of the following:
- Two opposing external side walls that are open from floor to ceiling.
- One external side wall fully open, as long as the length of the open wall is at least double the distance to the opposing wall.
- Vents are installed in both opposing external walls as long as: wall are 10 metres apart of less; there is a vent near the floor and near the ceiling every 2 metres; and there must be 0.1 sq metres of venting for each metre or wall, vents must be evenly distributed.
Gas monitors must measure carbon dioxide levels and/or oxygen in storage rooms containing argon or nitrogen. An audible and visible alarm should be installed both inside and outside the area.
Carbon Dioxide Toxicity:
As described in our blog Occupational Health Risks of Carbon Dioxide, never use an oxygen sensor as a method of measuring CO2, instead, always use a dedicated sensor for the measurement of carbon dioxide.
Air is primarily nitrogen with 20.9% oxygen, the quantity of CO2 required to displace the oxygen to a low alarm level of 19.5% O2 is approximately 70,000 ppm CO2. You will be overexposed to CO2 long before the oxygen sensor reaches its alarm point. CO2 levels as low as 3–5% can cause respiratory problems and headaches.
In Australia, the recognised exposure limits for CO2 reference an 8-hour Time Weighted Average (TWA) of 5,000 ppm and a 15-minute Short Term Exposure Limit (STEL) of 30,000 ppm. CO2 at 40,000 ppm is considered Immediately Dangerous to Life or Health (IDLH).
According to AS 5034, mandatory monitoring of CO2 must have an adequate alarm at TWA (0.5% Vol) and STEL (3% Vol). Alarms must sound when CO2 levels reach 1.5% and again at 3%.
Oxygen Depletion:
We all need to breathe the air to live; air is made up of several different gases including Oxygen. Normal ambient air contains an Oxygen concentration of 20.9% v/v. When the Oxygen level dips below 19.5%, the air is considered Oxygen-deficient.
In storage rooms where argon or nitrogen are used, levels of oxygen need to be monitored to ensure they remain above 19% Vol. An alarm must sound when oxygen levels fall below 19% Vol.
Training and Risk Management:
In addition to specifications on gas monitoring, the standard advises on elements of personnel training, operation, and maintenance; room size, gas location and ventilation; emergency procedures; signage and more.
Other ways to minimise risks:
- Inspect cylinder connections, pipes, and other equipment weekly or in accordance with manufacturers instructions.
- Follow a regular maintenance schedule, including 6 monthly calibrations.
- Minimise access to confined spaces to only those who are required to be there. Ensure they are fully trained.
- Provide training and/or complete all required training prior to operating equipment or handling cylinders.
- Keep signage and hazard labels clear and visible.
- Have the fewest number of cylinders onsite as possible. Ensure that they are well secured and stored in a safe area.
- Store gas cylinders outside, if possible.
- Provide easy access to protective equipment and breathing apparatus.
It is the responsibility of both the employer and the employee to prevent gas leaks. Following the regulations set out in AS 5034, being aware of the risks and communicating with others when hazards arise will all help to keep employees, employers, and members of the public safe.
CAC GAS specialises in gas products for gas detection, process gas analysis, environmental monitoring, and laboratory gas analysis applications. With distribution centres now in both Sydney and Singapore, CAC GAS is proud to provide their products and services globally.
Specialty and calibration gas mixtures are available in multiple cylinder sizes to meet customer requirements. A total solution provider, CAC GAS supplies gas generators, mixers, calibrators along with a complete gas control product range including regulators, outlet panel, manifolds, and gas distribution systems. Our products can be used anywhere calibration gases are required.
CAC GAS focuses on understanding customer requirements and providing solutions that exceed customer expectations.
For more information on how CAC GAS can help with you gas monitoring solutions, contact us at cac@cacgas.com.au.
Fast-Track Food Safety with 2-Hour Listeria Testing
When Neogen introduced its Molecular Detection Assay at the International Association for Food...
Serving Up Efficiency: Why AI is the Next Big Ingredient in Food Manufacturing
With margins tight and supply chains unpredictable, AI-powered systems are becoming the secret...
Optimized CO2 concentrations in greenhouses translate into higher productivity and higher quality
In greenhouses, the growth rate and development of all plants can be improved by controlling...