Atlas Copco's oil-free compressed air, nitrogen and carbon dioxide solutions for the food and beverage industry
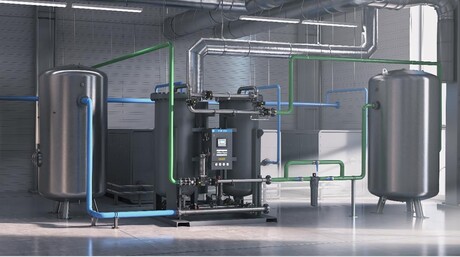
Compressed air is used in a broad range of applications in the food processing industries such as:
- mixing of ingredients;
- cuttings;
- spraying;
- drying of product; and
- transporting/propelling product through processing systems and packaging of final product.
In many of these applications, compressed air is in direct or indirect contact with food product. If not treated or incorrect technology selected, the impurities in the compressed air may contaminate the food product. This can result in change in colour and taste, reduced shelf life, in addition to exposure to bacteria and other microorganisms which can result in product recalls.
Nitrogen on-site generation solutions
Nitrogen is used in various food & beverage processing and packing applications for preservation and food safety. Atlas Copco on-site nitrogen generation can be combined with existing compressed air set-up or if you’re thinking about putting in a brand-new plant then nitrogen generation can be integrated along with your compressed air needs. Having on-site nitrogen generation at your doorstep gives huge benefits, not only operating cost reduction, but also on-demand supply, independence of third parties, peace-of-mind, and increased production uptime. By meeting erratic demand fluctuations, Atlas Copco PSA (Pressure-Swing-Adsorption) nitrogen generation offers a continuous production of nitrogen and nitrogen purity 99% to 99.999% to the application purity requirements.
Explore more about how to produce your own nitrogen on-site using Atlas Copco Nitrogen NGP+ PSA technology principle and six benefits of on-site gas generation.
Carbon Dioxide (CO2) recovery & compression solutions
Carbon Dioxide is widely used in many food & beverage processes — for example, a brewery. CO2 is generated as part of the fermentation process and used in a brewery’s final process, including all carbonated drinks. It is the major greenhouse gas (GHG) released into the atmosphere, and there is strong evidence that GHG is a cause of global warming.
From carbon dioxide recovery or generation from your processes, our CO2 oil-free compression (booster) and drying solutions safeguard the compressed CO2 quality for end product use. This reduces operating costs, and ensures on-demand supply, independence of third parties, peace-of-mind, and increased production uptime.
A case study of SP Italy shows CO2 to control insect pests in their production process to guarantee rice quality and safety. At the end of the process, instead of being released in the atmosphere, the CO2 is recovered up to 80%.
When producing beer, breweries conduct a whole process of malting, milling and mashing.
One of the steps is the fermentation of the yeast. Here, a low-pressure compressor supplies oxygen to bacteria which in turn creates alcohol using micro-organisms. During this process, CO2 is created and released.
Our recovery system can recover CO2 that would otherwise be lost and store it. Did you know approximately 4 kg of CO2 is produced per hectolitre of beer and to carbonate the same amount of beer, only 3 kg of CO2 is needed? It shows that breweries are not only able to sustain their own need of CO2 but additionally they can use it for other commercial goals.
This means on average the CO2 compressor will have paid back its investment in 2 years!
Carbon dioxide can be used for carbonating drinks, medical purposes, and MIG welding.
If your operation size starts from 500,000 hectolitres per year, the Atlas Copco CO2 compressor is the way to go. Let us help you:
- Save money by not having to invest in CO2 acquisitions
- Reduce your environmental impact by recycling CO2 emissions
- Receive local support 24/7
- Experience a return on investment after approximately 2 years
The high cost of not going green or not having the latest energy efficient technology
Today, the opportunity is green technology. And missing out on it will mean getting left behind. While it is true that the initial investment for some eco-friendly equipment may be higher, a reduction in production costs in the long run and other benefits will quickly recover that difference and more.
That is why the real question companies should be asking is not “What is it costing my company to go green?” but rather “What is it costing my company not going green?”
The answer is ‘a lot’
In our fast-paced world, being able to plan ahead is incredibly important to managers. In most cases, surprises are bad for business. Using older, inefficient equipment makes companies vulnerable to sudden, drastic changes, such as a new environmental law or a court ruling that bans certain machinery. Businesses that are ahead of their times with innovative, green technology do not have to worry about their equipment all of a sudden having to be replaced.
While each of these reasons should be compelling enough to get companies to go green, perhaps the best argument is that environment-friendly technology is inevitable. Each year, consumers will demand companies to be more responsible. Each year, environmental standards will get tougher. And each year a company fails to act, it is going to be left further behind.
You’re in luck today because we have 10 steps to a greener production. Best of all, some of them involve things you can do today and that will cost you hardly anything at all. By the end of the day, you could already be saving money.
If you want to know how, check out our new “10-step guide to a greener, better, and more efficient production” or watch our webinar.
Choosing a technology partner — Atlas Copco
Choosing a technology partner always entails some degree of risk. You can dramatically increase your chances of success by asking the right questions and be much more confident in your decision by thoroughly understanding the processes and technology used by your prospective partner.
Take advantage of what great partners can really offer — new strategic competencies. Whether you need strategic direction to help you innovate and compete, with the right partner, you can leverage the best and right technology available and instantly gain the capabilities for success, which can be capitalised and marketed. Reach out to one of our specialised consultants and let us educate you on a better tomorrow, today.
1800 023 469
Enhancing product safety and quality control with METTLER TOLEDO's inspection solutions
In the world of food manufacturing, ensuring the safety and quality of every product that reaches...
OD200: New Compact Distance Sensor Raising the Bar in Performance and Reliability
Launching in June 2025 from SICK’s HQ in Waldkirch, the new OD200 miniature distance sensor...
Heat and Control expands thermal range with Tek-Dry acquisition
Earlier this year, Heat and Control announced the acquisition of UK-based company Tek-Dry Systems...