In a puff: clean compressed air solutions
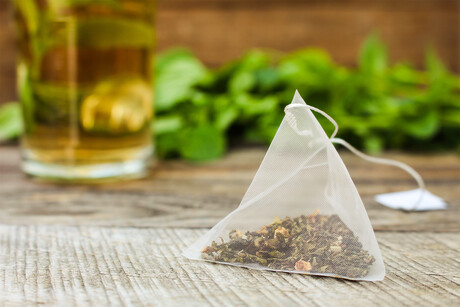
From baked beans to chocolate custard, tubes of toothpaste to bottled water, the filling in meat pies to the icing on cakes — all require a clean, high-quality, pressure-controlled supply of compressed air.
Even something as simple as a puff of air into a bag, so it can be filled with carrots, comes down to compressed air production. These are just a few examples, but for any supermarket product line one can think of, an air compressor will be involved at some — in fact multiple — stages of its life cycle. Fresh food, frozen goods, dried, dehydrated, marinated and pickled, canned, bottled, vacuum sealed and more — these are all functions that depend on an air compressor, humming away in the background.
Making tea bags
Australian green tea company ITO EN Australia has recently established a purpose-built manufacturing facility for production and packaging of its bagged green tea products, in north-east Victoria. The facility depends entirely on oil-free air compressors, with the key early design challenges being the essential need for supply of clean, high-quality, oil-free air. ITO EN Australia’s Manufacturing Coordinator, Rory Brooksbank, explained: “Tea bags have to be manufactured in a clean room environment, with all of the equipment associated with that manufacturing, producing clean dry air.” The process starts with a small pyramid-shaped tea bag, made from filtered material, that’s then filled with loose tea. Air cylinders can be seen darting in every direction to form the customised shape of the bag.
In addition to the compressors driving the pneumatics in those machines, the company needs a reliable and safe supply of nitrogen. “Nitrogen is produced outside, piped into the production room, then into the machine,” Brooksbank explained. “Inert nitrogen is injected into the tea bags for sterilisation. The nitrogen creates an oxygen-free environment in the bag, to prevent the green tea’s deterioration, as well as preventing bacterial growth.” The sterile tea bags are mechanically moved along the production line, placed and sealed with nitrogen into an envelope, sorted into 20-unit groups and packed into boxes.
Customised solutions
Jean-Philippe Leclercq is the Oil Free Air Specialist at Sullair and has worked with a number of food and beverage manufacturers, like ITO EN Australia, throughout his career. He is all too aware that customising the air compressor solutions to the unique needs of the product and its specific production cycle is pivotal. “In a factory you have the compressing side, then the filling, then the packing side — all of which require compressed air, at different pressures, for different purposes,” Leclercq said.
This is especially the case when it comes to oil-free air supply. Though Australian food standards regulations don’t specify a legal need for oil-free equipment in food manufacturing, this is not the case in some other countries, with international standards determining specifics around purity and contaminant levels (ISO 8573-1:2010). Broadly speaking, food safety regulations require that if a material is deemed as hazardous, an acceptable level of that material is predetermined as allowable (based on rigorous scientific testing and data). That being the case, it must be assumed then that until regulations in Australia around air quality in food manufacturing are developed, the acceptable oil level content must be 0%.
“Oil-free air supply is crucial,” said Leclercq, “because 99% of the time in the food production cycle, the air comes into contact with the product.” With oil-injected equipment — even with adequate filtration barriers in place — the chance of oil contamination is still present. Where ingestible products are concerned, this is a risk that no food manufacturer should be willing to take. As well as being a health and safety issue, the impact to a company and its brand could be disastrous.
Since the events of 2020, companies are now having to re-evaluate everything about the way they do business — from staffing to health and safety, production cycles to equipment and especially now, whether their current products and markets are even still viable to them. The issue of product safety has come under serious consideration — particularly for those wanting to grow the export side of their business. Understanding what the international standards are and how they are different to the Australian industry will be the key. In many countries, standards around oil-free status are strictly enforced and products that are produced on oil-injected equipment may not be approved for import.
Understanding the intricacies of the compressor’s function and applications — the right pressure, the specific air flow and the air quality — and the unique needs of the client is key to designing the right solution fit for purpose, for each individual case. “Air compressors are like the lungs for the business,” Leclercq said. “With compressed air, you really rely on the supplier to technically support you.” In a great partnership between the end user and the compressed air supplier, the application of experience and specialist knowledge makes all the difference.
Phone: 03 9703 9000
Rockwell Automation PointMax I/O
Rockwell Automation has released PointMax I/O, a flexible remote input/output (I/O) system...
NORD Drivesystems NXD tupH surface treatment
The NXD tupH surface treatment has been developed by NORD to make aluminium as resistant as...
igus D1 motor control with certified PROFINET
The igus D1 motor control can now be integrated into higher-level control systems from Siemens,...