Stepping up production of powder protein products
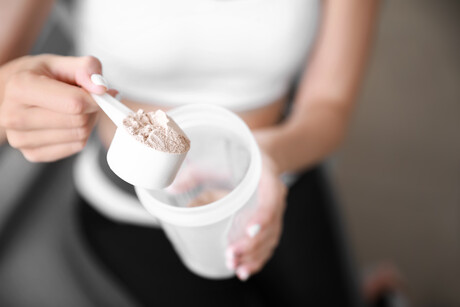
Discover how a leading Australian manufacturer of sports nutrition products implemented a system that enabled not only scalable growth potential, but also had the flexibility to handle an increasing range of ingredients.
True Protein is a family-owned business based in Sydney that manufactures a wide range of natural sports nutrition products, including protein powder blends and pre- and post-workout supplements. Established in 2014, the company now produces over 300 products and 12 protein flavours made from globally sourced ingredients.
Specialising in producing 100% natural products which have essential amino acids to assist muscle growth and healthy antioxidants, the company’s products contain no added sugar, artificial flavours or preservatives.
Prior to the implementation of the Matcon powder handling system, the company’s original process consisted of two lines:
- Line one comprised a small vertical mixer which was emptied by the operator into small drums. These drums were manually fed into a hopper which supplied a small screw conveyor filling a 250 g pouch auger packing machine.
- The second line consisted of a larger version of the first line. However, on this line there was a 600 L vertical mixer hopper feeding an inclined bucket elevator which in turn fed a 1 kg bag filler running at 6–8 bags per minute.
This production set-up was labour-intensive and inefficient with numerous manual handling process steps. Product recipe changeover was slow due to the amount of equipment cleaning needed when switching recipes and floor space was also tight, limiting the company to smaller volume, campaign-style production.
To meet an escalating order demand and growth ambitions, True Protein purchased a larger building next door to its existing premises to cater for its expected 50% growth in production capacity and sought a new production set-up that could support their requirements.
The solution
From the outset of project discussions, True Protein liked the simplicity and flexibility that the Matcon IBC system offered. The company could see the opportunity to improve efficiency and production capacity, whilst significantly reducing the number of manual handling steps. Future product formulations could also be easily introduced into the manufacturing process.
The Managing Director of True Protein, Ben Kierath, had previous experience of a Matcon system at a major company in Europe and recognised the benefits that could be achieved from installing a new Matcon IBC system, including:
- handling multiple flavours and batch sizes in one shift due to the quick changeover now possible during blending;
- reducing cleaning time as IBCs can be washed ‘offline’ before being put back into production;
- enhancing product integrity as previously hard-to-handle powders, such as whey powder, could now be discharged without risk of segregation using the Matcon Cone Valve.
The Matcon team worked closely with the team at True Protein to determine the most process efficient layout tailored to their needs and Matcon supported this by providing 3D model drawings. The existing building structure was put to good use — the mezzanine floor was used for the sack tipping of raw materials into the IBCs and the side wall was used for raw material storage.
Together a system was developed and designed to increase flexibility and efficiency of production, whilst also addressing the following key areas for improvement:
- Reduce manual handling
- Reduce down-times with off-line cleaning
- Rapid recipe changeovers
- Implement a system that enabled scalable growth potential and flexibility to handle a wider range of ingredients
The Matcon system included the following process equipment:
- A raw ingredient IBC Filling System that loads the batch ingredients into an IBC. These ingredients include whey powders, various flavours and minor ingredients.
- Multi-sized IBC Blender accommodating IBCs from 1000 to 1500 L
- Batch feed system discharging to a Pouch Packing Machine
- IBC Wet Wash System
- 1000 and 1500 L stainless steel IBCs
The benefits of the system include:
- Improved product security
- Faster recipe changeover and blending times
- Packing efficiency
The results
“Since going live with the Matcon IBC Blending System, True Protein’s manufacturing capabilities have become more streamlined and efficient. The Matcon system enables trusted cleaning procedures that gives us absolute confidence when it comes to changing from one formula to the next. Ensuring we eliminate any chances of allergen cross-contamination is essential to our business,” Kierath said.
“Creating a safe working environment is our number one priority at True Protein and installing a Matcon IBC Blending System has really contributed towards creating a safer workplace.
“The Matcon IBC Blending System allows us to blend much larger batches than our previous system, providing significantly increased efficiency due to reduced batch preparation, cleaning and blending times.”
Phone: 02 9892 4822
SIG recycle-ready, bag-in-box packaging for wine
SIG has partnered with Australian wine producers to produce a recycle-ready bag-in-box for wine.
BMT Blowscan and Thermoscan rPET bottle perfecting systems
Blowscan and Thermoscan are designed to help manufacturers improve PET bottle performance, reduce...
Henkel Loctite Liofol LA 7837/LA 6265 solvent-free adhesive system for packaging
The system is tailored for applications involving high thermal stresses — in particular...