Optimised system for bottle washing machine
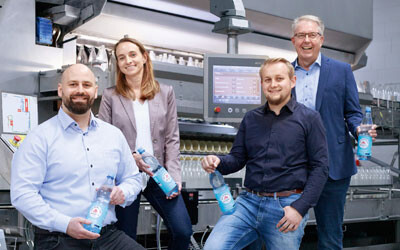
German mineral water bottling plant Staatlich Bad Meinberger has implemented KHS HASYTEC Dynamic Biofilm Protection. This is a system for bottle washing machines and pasteuriser, which is said to be reducing deposits on machines with ultrasound as well as lengthening cleaning intervals and shortening downtime.
Staatlich Bad Meinberger said the system reduces deposits of biofilm, limestone and fibrous material from paper labels in the spray pipes on the KHS Innoclean EE bottle washer, for example. In the past, without this system machinery often became clogged with deposits that required a considerable amount of effort to remove. “The combination of paper and limestone in particular presented us with a real challenge, our colleagues often had to get to work with a chisel!” said Jannis Maas, plant manager responsible for production and supply at Staatlich Bad Meinberger.
From shipbuilding to the beverage industry
The technology isn’t new. What is new is that a procedure that’s been in use for many years in a completely different sector, namely shipbuilding, is now being applied to the beverage industry. The system is a simple plug-and-produce product where ultrasonic transducers cause the liquid in certain components of the machine to gently vibrate. The system is currently available for both bottle washing machines and pasteurisers, whether for new machines or as a conversion for existing systems.
It’s not just the time-consuming physical labour that’s hard work when it comes to cleaning machine parts. In the peak season especially, with the plant running at full capacity, finding an appropriate slot for cleaning often proves something of a headache.
“Before we installed the ultrasonic converter, the level of calcification on the machine had to be checked at the latest every two months and the machine then descaled and partly dismantled in order to remove the deposits formed. This took up an entire day that had to be blocked off in the production schedule or moved to a weekend. And even if the team is basically motivated to put in a shift on a Saturday or Sunday during the peak season if this is necessary, they’re understandably not desperate to do this work that’s strenuous and unproductive,” Maas said.
The results
The system, complete with two control units and 12 ultrasonic transducers, has been in operation for about 18 months now.
In the end, the engineers’ curiosity won them over, resulting in the mineral water bottling plant being one of the first beverage operations to use this technology.
“We often filled an entire wheelbarrow with deposits in the past; now we barely need a 20 L bucket. And this year we haven’t yet had to carry out a single acid treatment. The system is completely autonomous and practically maintenance free,” said Robert Mühlenweg, technical and logistics plant manager for the beverage producer.
The mineral water plant is also being supported in its striving for greater sustainability by the use of the new procedure. “On the one hand, the Dynamic Biofilm Protection system considerably lengthens the time between cleaning operations and reduces downtime, thus enabling a significant increase in production,” said Kathrin Gareis, service product manager at KHS. “On the other, the consumption of water, heat, electricity and chemicals such as citric acid used to descale components is greatly decreased by this system. Besides the cuts in operating costs this results in, this also helps to save energy and resources — an issue which is so important to our customers.”
Phone: 03 9335 1211
SIG recycle-ready, bag-in-box packaging for wine
SIG has partnered with Australian wine producers to produce a recycle-ready bag-in-box for wine.
BMT Blowscan and Thermoscan rPET bottle perfecting systems
Blowscan and Thermoscan are designed to help manufacturers improve PET bottle performance, reduce...
Henkel Loctite Liofol LA 7837/LA 6265 solvent-free adhesive system for packaging
The system is tailored for applications involving high thermal stresses — in particular...