Bickford's improves bottling capacity with PET line
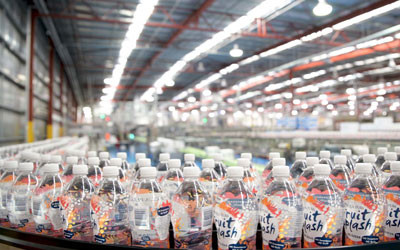
Bickford’s Australia has installed a complete, flexible aseptic PET line by Sidel in its Adelaide-based facility. The PET line can handle both sensitive beverages and carbonated soft drinks (CSD), improving production efficiency and sustainability. Founded in 1839, Bickford’s is now an independently owned business, exporting to 32 countries worldwide. The beverage manufacturer produces CSD, cordials, flavoured water, still and sparkling water, juices, dairy and non-dairy drinks, syrups and alcoholic beverages, such as beer, wine, spirits and cider.
Increasing health consciousness among consumers has driven the growth of beverage categories such as bottled water, while juices, nectars, soft drinks, isotonics and teas (JNSDIT) are predicted to show a positive trajectory in the future. New product developments in the beverage industry are increasingly focusing on new packaging formats for further diversification in the market. In the beverage industry, PET is projected to remain a consistently prevalent packaging material in future.
To accommodate these opportunities, Bickford’s sought a flexible production line that could handle both still and sparkling beverages, as well as low- and high-acid products with two different short bottle necks and two decoration possibilities.
“Previously, we were mainly familiar with hot-filling PET applications. We decided to partially shift to aseptic PET bottling because we wanted to optimise our production set-up and achieve a better total cost of ownership, which is of course critical if you plan to attract more consumers. Plus, we really wanted to diversify our product portfolio by introducing new references, including dairy products and plant-based alternatives, and by moving some drinks formerly packaged in glass and can to PET,” said Angelo Kotses, Bickford’s CEO and owner.
Bickford’s invested in one complete, versatile PET line, capable of managing both sensitive products and CSD through an Aseptic Combi Predis and a Combi SF300, respectively. This also helped Bickford’s enhance its packaging design, due to the PET line’s capacity to apply both sleeve labels and pressure sensitive labels. Sidel’s dry preform sterilisation technology provided an easy-to-operate and sustainable packaging solution for the beverage manufacturer. The PET line expands the company’s manufacturing capacity in terms of volume and type of beverages, while switching from one product to another, processing more than 20 different SKUs including still water, coffee with milk, coffee with almonds, four different flavoured waters and eight types of juices, all in either 250 mL, 500 mL or 1 L formats.
Throughout the project, Sidel collaborated with Bickford’s marketing team to launch their products. New containers were designed for Bickford’s 1L Aqua Pura branded water, applicable both to sparkling and still water, with the latter supported by a StarLITE base. Sidel also developed a 600 mL design, applicable to a variety of beverages, including flavoured water.
When redesigning the packaging, Bickford’s halved the weight of its 1 L juice bottle to 32 g and increased its shelf life by up to eight months, by changing the production set-up from hot-fill packaging to aseptic PET bottling with dry preform sterilisation. The new bottles are designed with straight body panels and simplified ribbing at the sides to allow the application of sleeve labels or PSL.
“To streamline our decision process, Sidel provided many bottle design alternatives and great conceptual designs with current labels as well as new prototypes. Considering the productivity advantages we gained and the high consumer acceptance around our redesigned containers, we are planning to strengthen the cooperation with Sidel further and launch a 1 L format for sparkling products, for water as well as CSD,” said Beverly Reeves, Senior Brand Manager at Bickford’s.
To install the aseptic PET production line, Bickford’s reorganised the production set-up and raw material localisation, by removing two out of three hot-fill lines, thereby gaining more floor space. The PET line, set up at the Adelaide plant, includes Tetra Pak processing systems technologies to provide product safety and increase uptime. The Aseptic Combi Predis also features the Capdis system for dry cap decontamination, with a compact and hygienic BlendFILL configuration that combines carbonator and filler in a single system for reduced consumption of CO2. Gebo OptiDry, a stainless steel drying system, was also integrated into the line, alongside Sidel’s Roll Adhesive labeller and a sleever intended to handle PSL.
The PET line can manage both aseptic and regular PET packaging on two different Combis, thus dealing with products featuring two bottle necks (28 mm for CSD and 38 mm for aseptically bottled products). Bickford’s chose one single end-of-line (EOL) solution to optimise the TCO, leading to maximised uptime due to simplified changeovers. The EOL also features a VersaWrap wraparound case packer and a PalAccess palletiser.
The line is capable of running at 12,000 bottles per hour (bph) for aseptically filled drinks, and up to 18,000 bph for CSD products, leading to a production capacity reaching approximately 60 million bottles per year.
“It is important to note that this fantastic opportunity to switch from one product to another is not compromising the sterility of our production, rather the opposite. The PET aseptic line in our factory runs 10 hours per day and Sidel managed to keep the product in the filler under complete food safety conditions between the last shift of the day and the first one the day after, meaning for more than 12 hours,” said George Kotses, Operations Manager at Bickford’s.
The Combi Predis PET line reduces the company’s environmental footprint, as it does not consume any water and uses very few chemicals. The reduced need for cleaning in place also lowers the PET line’s maintenance costs. Bickford’s first sellable product from the PET line was introduced to the market in the summer of 2019.
Phone: 02 9899 4642
SIG recycle-ready, bag-in-box packaging for wine
SIG has partnered with Australian wine producers to produce a recycle-ready bag-in-box for wine.
BMT Blowscan and Thermoscan rPET bottle perfecting systems
Blowscan and Thermoscan are designed to help manufacturers improve PET bottle performance, reduce...
Henkel Loctite Liofol LA 7837/LA 6265 solvent-free adhesive system for packaging
The system is tailored for applications involving high thermal stresses — in particular...