Asahi saving energy with water bottled using KHS technology
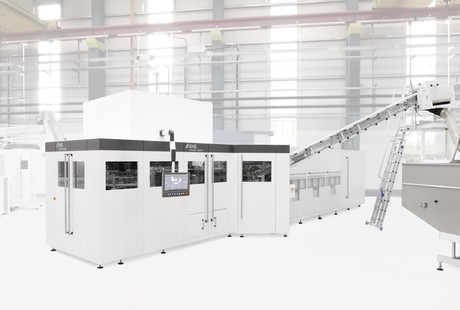
Asahi beer is a premium product that is now exported worldwide. Not so well known outside Japan — but no less important for the holding — is the local soft drinks and water market. In 2018, Asahi achieved a turnover of over 360 billion yen (around AU$4.9 billion) in this segment.
With over eight production sites, Asahi Soft Drinks has a selection of products ranging from ciders, teas and milk beverages to still and carbonated mineral waters. The company bottles its ‘Rokko No Mizu’ water at the location of the same name, which is not far from the cities of Kōbe and Osaka. Rokko was one of the first mineral waters produced, and today it’s filled into PET bottles to meet consumer demand for sustainable containers.
The company is now manufacturing the bottles using the KHS InnoPET Blomax Series V stretch blow moulder. Asahi Soft Drinks opted for this machine after seeing it exhibited at the BrauBeviale trade show in Nuremberg, Germany, in November 2018. This was also the case in 2008 when a prototype of the InnoPET Blomax Series IV found its way to Japan. Twelve years later the new and meanwhile established Series V is now producing 600-millilitre to-go bottles and large two-litre receptacles of still Rokko mineral water. Around 200 million containers a year are manufactured on the KHS system.
Energy consumption reduced by up to 40%
Asahi’s systems supplier from Dortmund has made a 40% reduction in energy consumption possible by including a number of further developments in its next generation of Blomaxes.
The Series V saves up to 40% in energy compared to its predecessor through the implementation of an optional new heating concept. The near infrared (or NIR) heater centrally installed in the closed reflector tunnel forms the nucleus of this. In the heater the preforms pass the centrally arranged heating units to both the left and right. This means that every single NIR heater is used twice, so to speak.
In the Series V, KHS has supplemented its patented AirbackPlus air recycling system for an up to 40% saving in compressed air with its new EcoDry air management system. This uses the residual air from the blowing and recycling process to replace a separate air drier in the base mould area and in the blow wheel, again yielding significant savings in energy.
Asahi has recently announced that plans for a second stretch blow moulder from the new series are already underway.
Phone: 03 9335 1211
SIG recycle-ready, bag-in-box packaging for wine
SIG has partnered with Australian wine producers to produce a recycle-ready bag-in-box for wine.
BMT Blowscan and Thermoscan rPET bottle perfecting systems
Blowscan and Thermoscan are designed to help manufacturers improve PET bottle performance, reduce...
Henkel Loctite Liofol LA 7837/LA 6265 solvent-free adhesive system for packaging
The system is tailored for applications involving high thermal stresses — in particular...