Facility upgrade transforms beef supply chain logistics
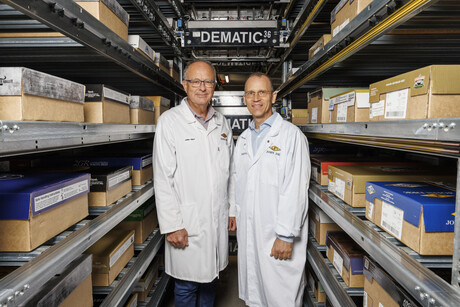
Dematic has worked with John Dee, a family-owned Australian beef producer, to help transform its operations to meet the evolving demands of global beef markets.
John Dee’s Warwick-based processing plant in Queensland, strategically located on the Darling Downs, just two hours from the port of Brisbane, is instrumental in supplying premium beef cuts to more than 145 customers in over 37 export markets worldwide. Over the years, it has evolved from a local beef producer into a major beef exporter servicing a diverse range of international markets.
“We’ve been a beef processor in Warwick since 1945, and today we’ve transformed into a full-blown beef export and processing operation,” explained John Hart, Owner of John Dee, Warwick. “In the early days, we sold full sets of meat parts, whereas today we break them up and send different components to Japan, Korea, Indonesia, Taiwan, the EU and America.”
With growing demand, especially from international markets, John Dee faced a critical challenge. The company had outgrown its existing storage capacity, and manual operations were proving inadequate to meet the complexity and scale of their production.
“With the way we’re operating today, trying to get product into the right place at the right time, it was becoming almost impossible to do it by hand,” Hart said. “In our previous manual operation, people had to understand all the product codes and pick by hand out of a cold store. With over 10,000 cartons being produced a day, it became a logistical nightmare. A thousand cartons a year that would go out of date because they couldn’t be located.”
In response to these challenges, John Dee embarked on a multi-staged facility upgrade project, partnering with Wiley and Dematic to design and implement automated systems tailored to their unique needs. At the heart of the transformation is the Dematic Multishuttle Meat Buffer Storage and Handling System, a solution specifically designed to address the complexities of meat processing. The system automates the storage and retrieval of product cartons, streamlining operations in sub-zero conditions. It manages products both chilled to -1°C and frozen at -20°C, reducing the reliance on manual labour in harsh cold store and freezer environments.
“Our advanced Dematic Multishuttle system provides a high-performance, accurate, safe and cost-effective automated order fulfilment and despatch processing solution for the meat industry, and we are very excited to see John Dee reaping the many benefits at their Warwick facility,” said Soeren Schauki, Business Development Manager at Dematic. “The system was completely operational at full speed on day one, and the throughput of this system is unmatched.”
Operation of the four-aisle, 30-level Multishuttle is managed by Dematic Warehouse Control System (WCS) software that provides full track and trace, where each carton is followed throughout the supply chain, so losing product is no longer possible. The WCS also controls the storage duration of all cartons, allowing John Dee to set the time each carton can remain in the system. This helps to improve the shelf life of the meat products and is designed to ensure cold chain compliance is maintained.
The solution is designed for John Dee to scale up and increase its premium beef export market share. One of the frozen aisles can also be switched to chilled in response to anticipated future growth and advancements in cold supply chain export markets across Asia.
“In working with Dematic, we ensured that our system would be able to adapt for the future growth of John Dee to increase capacity to match significant surges in demand, whilst also providing improved worker safety,” Hart said.
Since implementing the new system, John Dee has reduced its reliance on labour, which, in a tight labour market, has become difficult to source for harsh cold storage facilities. In doing so, John Dee has reduced occupational health and safety issues associated with employees working in a cold storage environment.
“Our recent expansion of our Warwick facility is the largest single investment in the company’s almost 80-year history, and it is supporting our business growth and competitiveness during a time when beef exports are rising significantly,” Hart said.
Video: Sub-zero supply chain optimisation with automated meat storage & handling
Phone: 02 9486 5555
Key Technology COMPASS Belt-Fed Optical Sorters
Key Technology introduces the COMPASS belt-fed optical sorters.
Olivo multi-temperature food transport solution
CoolPac has introduced Olivo insulated food containers, which are designed for the transportation...