Calculating 'safety stock' the key to minimising supply chain risk
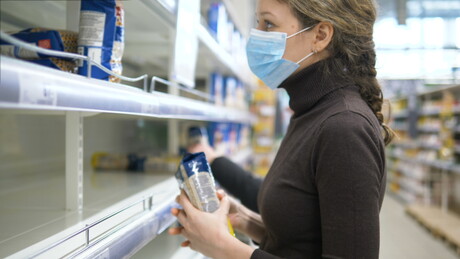
According to the ABS, the retail surge in March is the strongest rise since it began tracking retail trade. While the panic buying saw empty shelves in supermarkets across the country, what often goes unseen are the Australian manufacturers behind the scenes struggling to fill this unprecedented demand.
“Determining appropriate inventory levels is one of the most important and most challenging tasks faced by supply chain managers,” said Levi Martins, SAGE Group company Nukon’s Senior Consultant & Support Lead.
“If you carry too much inventory, you tie up money in working capital and risk writing off perishable goods; if you don’t carry enough inventory, you face stockouts.”
What is safety stock?
In any supply chain planning, safety stock (sometimes known as ‘buffer stock’) is extra stock to cover demand or supply variability and to avoid stockouts.
Stockouts stem from factors such as:
- fluctuating customer demand, as we’ve seen during the pandemic;
- forecast inaccuracy;
- variability in lead times for raw materials or manufacturing.
Having adequate safety stock levels enables business operations to continue production according to their plans.
Think of safety stock as serving as a type of insurance against unplanned supply chain events. For example, a supplier may deliver their product late, the warehouse may be understaffed or items may be received that are below the usual level of quality. There’s also the chance that a competitor may be sold out on a product line, which leads to increasing demand for your own product.
“The cycle stock portion of the inventory equation might be straightforward. But what really keeps people up at night is safety stock, and how to determine the appropriate levels,” Levi said.
Safety stock enables organisations to satisfy customer demand in the event of these variables.
Panic buying during March and April of 2020 saw many manufacturers facing high levels of variables, forcing rapid changes to the planning process to meet increased demand.
Some operations managers rely on gut feelings or hunches to set safety stock levels, while others base them on a portion of cycle stock levels — such as 15 or 25%. While they are easy to execute, these techniques generally result in poor performance or leave you with other stock management issues.
The food and beverage industry can pose unique challenges for inventory management such as spoilage, seasonality and volatile consumer demand. Perishable products make the game even more challenging because they are particularly susceptible to spoilage, especially if there are improper storage conditions.
Safety stock determinations are not intended to eliminate all stockouts — but they can reduce many of them. While designing for a higher service level would result in fewer stockouts, this requires significantly more safety stock. There must be a balance between inventory costs and customer service. By using different methods and equations, you can still find safety stock levels that help you achieve your desired customer service levels.
Safety days of supply
Being profitable in these scenarios is reliant on the proper management of inventory, and this is where supply chain planners are the behind-the-scenes rock stars. Using a formulaic approach to safety stock helps rationalise the required levels of inventory to the business, while balancing the need to deliver on customer service and minimising costs of higher stock on hand levels.
So, its obvious planners and decision-makers need to be on the same page when it comes to inventory policy. Inventory issues are one of the biggest problems impacting profitability in manufacturing.
Developing production plans by simply dividing annual demand by the number of forecast periods has been the approach for many food and beverage companies, but this doesn’t take seasonality, trends, cost of production and carrying costs into account.
Other companies will base their figures on ‘safety days of supply’ (or safety coverage). The days of supply refers to the number of days of demand that your safety stock can service. The days of supply may include the inventory held to satisfy certain and uncertain demands.
To calculate how much you should produce or purchase against safety days of supply, you need to sum the projected demand for the next ‘safety days’ number of days. So, if you set a product to have five days of supply, expect the safety stock to be equal to the sum of the next five days of demand.
Once you’ve set a safety days coverage, you should also calculate your number of days of supply. This is calculated against your current holdings, asking the question “If I didn’t receive any other supply, how many days would I have before running out of stock?”
Sadly, Excel (which is the number one tool used by supply chain planners) doesn’t have the simplest formulas to calculate safety days or days’ supply. This means planners tend to use static approximate safety stock calculations, since this is what they can produce in a spreadsheet.
Supply chain planners need an easy-to-use system that can perform the calculations quickly and generate credible results. The results of having an effective system, combined with the forecasting and planning knowledge within your team, are significant.
Improving the supply chain planning process
One way to simplify the process around safety stock and general stock planning is to use the right tools. That way, you can not only stay on top of planning, but take advantage of other features to fine-tune your forecasting.
The biggest benefit of having a tool for supply chain planning, among other features, is being able to clearly see the stock levels and quickly calculating safety days in one application.
SAGE Group company Nukon has a number of clients who already use its planning solution called TilliT Planner to address their production planning challenges. When developing this part of the software suite, the team at Nukon made sure safety days of supply was one of the features. The software can draw on the real-time existing stock levels and customer demand to calculate the correct stock needed to be covered. All calculations are made for the user, instead of having to refer to multiple spreadsheets and formulas. The software is also customisable to help solve complex supply chain problems.
Phone: 1300 909 360
Olivo multi-temperature food transport solution
CoolPac has introduced Olivo insulated food containers, which are designed for the transportation...
Qimarox PR15 machine for unloading vertical buffer systems
The Qimarox PR15 machine for emptying vertical buffers comprises a vertically mobile...