An inside look into London's second-largest brewery
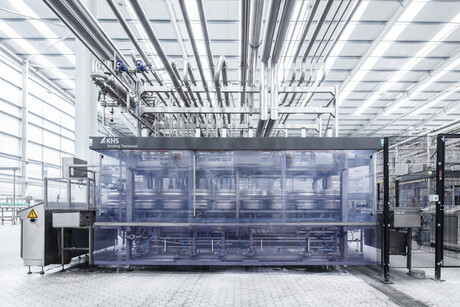
Logan Plant’s love of beer was sparked by his famous father, Robert Plant, lead singer of British rock band Led Zeppelin. Logan was only 18 when his father began taking him to the pubs of the British West Midlands, and by the time he was 20, he wanted to open his own brewery. Instead, he set off traveling the world with his band, only discovering local craft beer while on tour in the USA. It rekindled his idea of starting a brewery and Logan subsequently opened a pub in the London suburb of Haggerston, where he sold his own home brew. The project took off and evolved into the Beavertown company, which recently constructed a large brewery with the help of Dortmund-based KHS technology.
Logan Plant’s first brewing experiments were performed in his kitchen less than 10 years ago, using a rice pan and tea urn to make beer that was initially sold in his own pub. According to Beavertown Brewery, it is now the second-largest out of over 100 breweries in London. It operates several other facilities, including a microbrewery in the local stadium belonging to Tottenham Hotspur Football Club. Its most recent addition was a production site in the North London borough of Enfield.
Nikola Marjanovic, Beavertown Brewery Operations Director, labels this as one of the most ambitious projects to emerge on the British Brewery scene for years. With the aim to build a modern and unique brewery, the cost of investment was around £40m (AU$72m).
The brewery chose KHS to support its project in its early days and has been in contact with Andy Carter, Managing Director of KHS in Great Britain and Ireland, and his team since then.
To meet the demand for its own craft beer brands such as Neck Oil Session IPA or Heavy Gravity Hazy IPA, the decision to build a production plant was made.
Heineken was approached for support in the project, and after initially holding 49% of shares, now owns 100%. Despite this, Marjanovic said Beavertown still operates independently and has ambitious growth targets.
The percentage increase in the amount of beer produced has run into double figures in recent years, and the brewery aims to boost this by a further 30% in 2023.
KHS provided the brewery with the appropriate filling and packing technology to suit its requirements, which Marjanovic labelled an “advantage” as it meant all turnkey lines were sourced from a single supplier.
The premises were designed to centre on the keg and beverage can container segments with the aim of boosting performance capacity and configuring production for further growth.
“Our systems are flexibly adapted to cater for future requirements,” Carter said. “Thanks to their modular design, KHS machines can be easily retrofitted to meet a new increase in capacity or enable any adjustments that may need to be made to the secondary packaging, for example. A high standard of hygiene and low use of resources round off the list of requirements.”
The brewery invested in a turnkey canning line from KHS. Its integrated Innofill Can DVD filler that includes a Ferrum seamer is designed to process up to 33,000 330-mL containers an hour and available with an output of up to 135,000 cans per hour. A CO2 purging process ensures low oxygen pickup and consumption.
The line is supplemented by the Innoket Neo labelling unit and a fully automatic KHS Innopack Kisters WP Advanced wraparound packaging machine. The labelling station has cut the beer’s time to market and allowed smaller batches to be produced as no large quantities of printed cans are kept in stock. The packaging and palletising section is rounded off by the Innopal PB N palletiser and Innopal LD Z depalletiser.
In addition to beverage canning, the brewery also invests in KHS technology to process its kegs. It uses the Innokeg Transomat 6/1 Duo, a keg washing and racking system with two docked linear machines. This manages up to 160 kegs per hour holding between 30 and 50 L and includes options that can expand capacity to up to 240 kegs an hour.
The machinery uses pulsed sprays to ensure microbiological safety and product purity and uses counterflow cleaning in the pre-washer.
The conveyor belt in the modular Innokeg Transversal pre-washer segment runs through the middle of the processing machine, a function that can be deactivated if operators process one-way kegs. The kegs are then conveyed to the next machine without being processed.
The system may also contribute to reaching sustainability targets, with the Direct Flow Control (DFC) filling system designed to save on CO2 usage. Sustainability is at the centre of Beavertown Brewery and it aims to invest in a new water treatment plant and solar technology.
Despite considerable restrictions imposed by Brexit and COVID-19, the production site was completed within an agreed time frame. KHS’s ReDiS remote maintenance system was used to troubleshoot issues and resolve them with engineers at KHS head office.
“The new production site with its KHS lines is a real flagship for the brewing industry in London,” Marjanovic said.
Phone: 03 9335 1211
Geotab Cold Chain Solution
Geotab Cold Chain Solution with new hardware and enhanced software features is designed to boost...
Engineering services for food and beverage manufacturing facilities
With an in-house engineering team specialising in food and beverage process engineering, Total...
ADVANTEC Narrow Impingement Freezer
JBT launches the ADVANTEC Narrow Impingement Freezer that is suitable for small spaces.