Pork producer cuts emissions with onsite sludge treatment
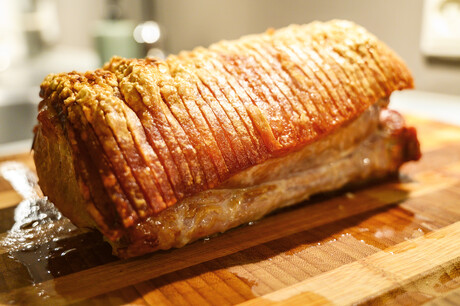
Pilgrim’s UK wanted to reduce sludge transport costs at its pork processing plant so it employed WCS Environmental Engineering (WCSEE) to help with that task. It has now trialled a new system that has resulted in not only lower carbon emissions but also green energy generation.
The challenge
Pilgrim’s UK already treats its own wastewater, which is processed through a dissolved air floatation (DAF) treatment system to meet high environmental trade effluent consents. A by-product of the DAF process is liquid sludge, which was historically collected from the plant and transported offsite up to six times a week for further processing by the site’s waste management company. This was costing the site not only time and money but also carried a high carbon footprint.
Andrew Hill, Site Services Manager at Pilgrim’s UK, said, “Pilgrim’s UK has ambitions to reduce its carbon footprint as part of its pledge to become net zero and reduce onsite waste through design and implementation of circular economy processes. The engineering team wanted to investigate the possibility of dewatering onsite, to reduce the cost of transportation and carbon emissions, and to see whether the dewatered sludge could be useful or had value.”
The solution
WCSEE carried out a laboratory test and analysis to find out more about the composition of the sludge and understand treatment options.
The technical team at WCSEE then designed and developed optimal chemical and mechanical treatment options to economically process the sludge at the plant located in Spalding, UK. This involved a trial installation of the screw press for five days to demonstrate its dewatering and sludge thickening capability.
The screw press model supplied was specified to meet the volumes of sludge the site was producing along with the correct blend of chemicals and precise dosing measurements. The plant was also assessed to identify the best location and configuration for the Volute Screw Press, including access to power and water.
A 6 m containerised unit, constructed offsite, was placed inside the existing processing plant containing everything needed to start processing the sludge.
“With the screw press’s plug-and-play capabilities, the team quickly adapted to the technology, and after a five-day trial period, it was decided to extend the trial by directly renting the unit from WCSEE, to further understand the return on investment,” Hill said.
The results
The trial showed that the dewatered sludge produced at the Spalding site had a potential gas yield that could be used to generate biogas electricity. Pilgrim’s UK was able to send the dewatered sludge to the nearest anaerobic digestion (AD) plant which proved to have such a high gas yield that it was valuable feedstock for biogas electricity generation.
Since the installation of the screw press, Pilgrim’s UK has seen more than an 80% reduction in sludge volumes overall and is now only sending dewatered sludge cake from the AD plant once a week on average. This process is now operating at zero cost due to its high biogas electricity generation value.
The Volute Screw Press is used for thickening and dewatering of DAF sludge with the addition of a self-cleaning filter that prevents clogging and enables constant dewatering without using large volumes of water. This delivers stable and constant dewatering, achieving up to 99% efficiency savings against belt presses and 92% against conventional screw presses.
Operated automatically by a 24-hour sensor control, if required, the Volute Screw Press is claimed to also require 70% of the footprint of standard screw presses and 5% of the power usage of a comparable centrifuge.
WCSEE now has an ongoing relationship with Pilgrim’s UK, which includes repair and maintenance along with chemical support with an optimised polymer used for the dewatering process.
Zooss Consulting Waste Buster forecasting tool to help reduce food waste
Zooss Consulting has launched Waste Buster, a smart forecasting tool designed to help food...
Eco-Products Vanguard packaging range
Detpak has released a range of compostable, no-added PFAS sugarcane plates, bowls and containers.
Mondi FunctionalBarrier Paper Ultimate high-barrier paper packaging
Mondi is expanding its FunctionalBarrier Paper range with FunctionalBarrier Paper Ultimate, an...