Digital manufacturing: intelligent sensors mean smart machine tools
By Boerge Wegner, Technical Industry Manager for Machine Tools in the Factory Automation Global Industry Center at SICK AG, Waldkirch
Monday, 01 July, 2019
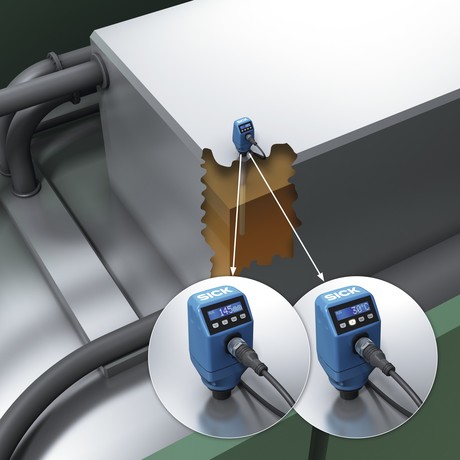
The smart factory is becoming a reality in more and more sectors — including the machine tool industry. Intelligent sensors which do not just collect data, but can also interpret and communicate it, are the crucial technological driving force behind the development. SICK’s range of Smart Sensor Solutions also gives the option of carrying out automation functions, known as Smart Tasks, remotely. This increases the flexibility, transparency, efficiency, quality, and availability of machine tools and makes it possible to align toward future requirements of Industry 4.0.
Monitoring the tension of multi-jaw clamping chucks, checking the tool position in multi-level die-casting units, checking that workpieces are being held correctly in defined machining positions, or monitoring drill lengths — these are just a few examples of where intelligent sensors with the Smart Tasks functionality can carry out different checking and automation functions in the sensor. Logic functions integrated into the sensors for processing signals form the basis of this, building on proven sensor technologies with best-in-class detection capabilities. These make it possible to carry out defined tasks autonomously and remotely, meaning that automation systems and networks of machine tools can be relieved effectively.
What sets Smart Sensors apart?
Sensors are generally the sensory organs of machines — in the context of digitised manufacturing, they are also the initial contact with and link to Industry 4.0. Whereas the aim in the past was to collect data and make simple decisions, today’s sensor intelligence also enables data to be prepared, further processed, and interpreted. Sensors, therefore, no longer just “sense”. Within the scope of digitisation, they are also starting to “think”. As a result, they convert data into valuable information. The option to communicate this information supplements the intelligence of these Smart Sensors. In other words, they can exchange information with the control of a machine tool or a cloud-based application for predictive maintenance, for example.
Smart Sensors provide added value for machine tools
Intelligent sensors, which can communicate, therefore offer key advantages in digital manufacturing straight from the factory. They become smart — and that is the unique selling point of Smart Sensor Solutions from SICK — as a result of the extensive options mentioned above for self-diagnostics and process diagnostics and, most notably, as a result of the logic functions integrated into the sensors for processing signals. Depending on the requirement and task, the advantages of Smart Sensors for digital manufacturing can cover up to four dimensions.
The Enhanced Sensing feature of the Smart Sensor Solutions provides extra detection performance if required. The refrigerant and cutting-oil-resistant IMB inductive proximity sensor, used in CNC machining centres, tool changers, and workpiece handling, offers increased sensing ranges, meaning that machines can be integrated as effectively as possible. With their TwinEye-Technology, photoelectric retro-reflective sensors, like those from the W16 product family, achieve the highest levels of operational safety as detection is carried out using two logically linked receivers in the sensor. The sensor only switches to the output state when both “eyes” come to the same evaluation. Switching errors due to shiny metal surfaces which reflect the light in different directions, for example, are therefore reliably avoided. When monitoring coolants and lubricants in machine tools, the CFP Cubic level sensor does not just measure the levels of water-based and oil-based media — it also provides information on the temperature, which can be used without the need for additional effort in the design phase and additional process monitoring costs.
Efficient Communication is the second dimension of Smart Sensors, which becomes apparent with analogue signal transmission. It is based on the bidirectional IO-Link communication standard and is carried out via standard M12 cables in parallel to the usual IO communication in the machine tool. When it comes to analogue position monitoring — for example, monitoring the tension of multi-jaw clamping chucks with magnetic cylinder sensors from the MPS product family — or checking the tool position in IMC inductive proximity sensors, data transmission via IO-Link means that the corresponding analogue cards no longer need to be used in the automation system. What’s more, Efficient Communication can accelerate a commissioning process considerably — for example, when several IMCs are used to check the position of a tool. Settings can now be made simultaneously via IO-Link and no longer need to be made successively and individually at each switch, which is incredibly time-consuming.
The diagnostics function is designed to enable the self-monitoring of the sensor. On top of this, it checks the quality and reliability of the sensor’s signals independently. In digital manufacturing, diagnostics functions also provide the possibility to significantly improve the availability of machine tools and quality of machining processes through status monitoring. The current trends focus on sensors, such as the CFP Cubic mentioned above, and rotative motor feedback systems in axle drives, which can record additional measurands or process variables on top of the measurands for which they were primarily developed. One of the main reasons for this is that they provide additional functions without additional costs. Sensors like the IQC inductive proximity sensors with up to four individual switching points or switching windows can also be used for diagnostics purposes — they can measure distances, interpret them as OK or not OK, and therefore detect tolerance errors in the forming processes, for example, during the inline quality control.
The decentralised computing power of Smart Sensors, combined with their flexible programmability, lays the foundation for a multitude of Smart Tasks, which make the machine tools even more flexible, dynamic, and efficient. A typical function of this kind might be high-speed counting. By using inductive and opto-electronic sensors, for example, it is possible to record and control rotating speeds or identify directions of rotation. The signals are evaluated in the sensors themselves — there is no need for any central counter modules. No pulses are output to the control — only rotating speed or speed values that are immediately ready for further processing. Smart Tasks such as time and length measurement, the remote debouncing of sensor signals, or time-stamp functions play a somewhat secondary role with machine tools. The opposite can be said of other subjects — tool positioning through distance measurement with micrometre precision; monitoring the width, edge position, and surface cutouts when winding and unwinding steel and aluminium coils and other web materials; checking the workpiece clamping; or monitoring drill lengths and tool dimensions to name a few. Intelligent, Smart-Task-enabled sensors can carry out all of these functions independently — and directly network with one another to resolve partial applications autonomously, quickly, efficiently, and cost-effectively without extensive PLC communication. When it comes to implementing Industry 4.0, they therefore create the possibility for cyber-physical production systems (CPPS) to communicate with one another and control one another. As intelligent items of operating equipment, these systems mean that production can be controlled in a remote, reactive, and adaptable manner, for example.
Smart Sensors are shaking things up
Intelligence and communication capabilities — on the one hand, the potential of Smart Sensors is incremental. They are oriented toward gradual increases in efficiency for the tasks at hand, such as downloading parameters for the fast changeover, easy device replacement, formula management, and condition monitoring. With the Smart Tasks, the Smart Sensor Solutions now have a radical component. With their remote intelligence, they can generate new, higher-quality detection information, network, and carry out defined Smart Tasks autonomously.
All of this makes SICK’s Smart Sensor Solutions a highly forward-facing technology — with the potential to shake things up for the further, progressive digitisation of manufacturing.
For more information, click here.
Enhancing product safety and quality control with METTLER TOLEDO's inspection solutions
In the world of food manufacturing, ensuring the safety and quality of every product that reaches...
OD200: New Compact Distance Sensor Raising the Bar in Performance and Reliability
Launching in June 2025 from SICK’s HQ in Waldkirch, the new OD200 miniature distance sensor...
Heat and Control expands thermal range with Tek-Dry acquisition
Earlier this year, Heat and Control announced the acquisition of UK-based company Tek-Dry Systems...