Compressed air considerations for food industry applications
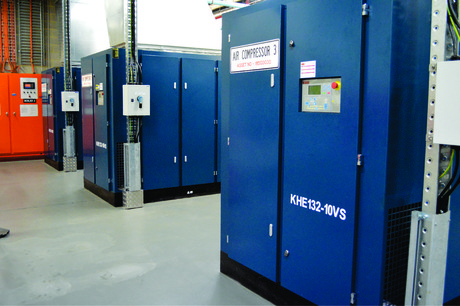
Most of Australia’s food processing and packaging industries rely on compressed air to provide power for production demands which vary greatly from industry type to seasonal variations. The selection of the right air compressor and system to match such needs is critical, not only for maximum productivity but to minimise the impact of rising energy costs.
Today, with the introduction of new technologies in a wider and more sophisticated range of compressors and ancillary equipment, every operator has the opportunity to select a compressor that will match their application requirements immediately and into the future.
FOOD GRADE AIR PRODUCTION
Due consideration must also be given to the quality and cleanliness of air being generated through the compressor and ancillary equipment. Potential contaminants such as dust, pollens, hydrocarbons, oil, moisture and other impurities can come from ambient air, lubricants and other pollutants in the air reticulation system which can also cause costly damage to downstream equipment as well as product spoilage, so it is important that compressors output ‘Food Grade Air’.
Martin Curd, Sales Manager of Southern Cross Compressors, explained: “Using high quality coalescing and carbon filtration backed up by the use of a residual lubricant sensor to monitor compressed air and log (record) the hydrocarbon levels, the highest level of air quality can be achieved and sustained. At Southern Cross we use ‘STELLA’ Food Grade Synthetic PAO Compressor Lubricant which is food-safe, non-toxic, and developed for rotary compressors used in the food, drink and pharmaceutical processing and packaging industries to meet all NSF H1 \ Food Grade \ Food-safe standards for the use in HACCP Certified Food and Packaging Manufacturing Plants. Our FGO series filters are engineered to ensure the highest quality compressed air for food industry applications. The highly efficient FGO range of filters are designed for the highest contaminant retention (99.9999% efficiency) with minimal pressure drop resulting in premium quality compressed air with reduced operating costs.”
Martin said, “An example of this is an iconic regional Victorian food production plant that recently installed a third large Southern Cross KHE series, two stage compressor to cater to increased production and compressed air demands. Each compressor is connected into the system through dedicated filtration and drying equipment to provide extremely high quality air to the processes. Each compressor operates with a food grade synthetic lubricant and although the compressed air does not come into contact with the product, the air is considered highly suitable for food processing.”
VARIABLE AIR SUPPLY DEMANDS
Within such a diverse range of production demands and multiple applications, it is highly beneficial both in delivering ample power to match each production phase whilst not wasting valuable energy when pauses or minimum outputs are required. By introducing Variable Speed Control (VSD) to single or multiple, in-line air compressors each compressor can be easily programmed and controlled to exactly match production scheduling. Martin stated: “This can amount to enormous energy savings, every day, whilst not affecting continued production at maximum efficiency. It also reduces unnecessary constant demands on the whole system that reduce machinery life and increase maintenance costs and downtime.”
SINGLE OR TWO STAGE COMPRESSORS
Many larger food industries are opting to upgrade to new generation, two stage rotary screw air compressors which can more than match required air generation with less energy input, and that means considerable savings in energy costs.
“Our two stage machines operate under far lower bearing loads which means lower maintenance requirements and lower likelihood of breakdown. They just purr along! Combine the two stage air compressors with VSD and the energy savings offer surprisingly fast payback on capital expenditure,” Martin added.
CUSTOMISED COMPRESSOR OPTIONS
For specialised food industry applications, air compressors can be designed or adapted to suit environmental conditions, required air quality, demand variability and other considerations.
Mark Ferguson, CEO of Southern Cross Compressors, stated: “We get many requests that require innovative solutions. Recently we utilised special components and stainless steel cabinets to supply Huon Aquaculture with seven rotary screw (KHE) compressors to run their sea based operations.” (See case study below.)
“We also assisted a salad mix grower to develop a revolutionary colour sorter, air jet cleaning system to ensure his product was perfect for his export market. Our design technicians are experienced at providing application specific solutions for food and other specialised applications.”
SERVICING AND MAINTENANCE
However, specifying the right replacement compressor alone won’t maximise efficiency, cost saving and air quality unless the air delivery lines, couplings and ancillary equipment such as filters, dryers and receivers are also well maintained.
For this purpose, Southern Cross conduct a complete system survey to detect leaks and any inefficiencies that require fixing to gain maximum performance and energy cost savings from every new installation. To ensure continued, trouble free and cost efficiency of the air compressor and systems, Southern Cross provide customised customer maintenance programs.
Mark added: “We are so confident in the durability of our complete KHE Rotary Screw range that we offer our customers a Lifetime Airend Warranty.”
**************************************************
HUON AQUACULTURE: Salmon Farming
Compressed air links innovative aquaculture operations.
Having utilised compressed air in their land-based operations for years, Huon Aquaculture Tasmania have successfully trialled the use of compressed air in their sea-based operations.
Huon commissioned 37KW Southern Cross KHE compressors on feed barges at the centre of each major pen configuration to power the salmon recovery from pens to the feed barges. This innovation has proven highly successful allowing remote selection of up to 12 separate pens to be centrally and individually controlled. With Huon’s ever evolving innovation and development of safer and more efficient systems, management have now opted to upgrade and replace these well worked compressors with seven new models. Working with Southern Cross designers and technicians, the new Huon customised compressors will utilise a high level of stainless steel componentry and be fully encased in stainless steel cabinets to better weather the extreme off shore conditions encountered in the salmon farm environment.
David Morehead, General Manager of Marine Operations at Huon, stated: “After experiencing the reliability and efficiency of the older compressors, we had no hesitation in working with Southern Cross to replace them with new KHE series compressors adapted specifically to our needs. We would expect the new compressors to serve us well into the future.”
Enhancing product safety and quality control with METTLER TOLEDO's inspection solutions
In the world of food manufacturing, ensuring the safety and quality of every product that reaches...
OD200: New Compact Distance Sensor Raising the Bar in Performance and Reliability
Launching in June 2025 from SICK’s HQ in Waldkirch, the new OD200 miniature distance sensor...
Heat and Control expands thermal range with Tek-Dry acquisition
Earlier this year, Heat and Control announced the acquisition of UK-based company Tek-Dry Systems...