An action plan for unprecedented times
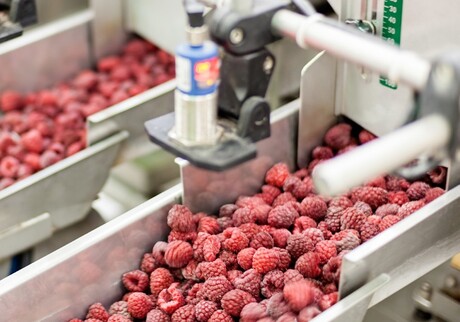
Food and beverage is often referred to as the “fast-moving consumer goods industry” — and that was before the worldwide health crisis created an economic disruption on a scale unseen for generations. Now ‘agility’ has taken on a whole new meaning as we navigate highly-unusual working conditions, unprecedented market dynamics, and disrupted supply chains.
You may be asking yourself some of the same questions we are:
- How can we do a better job operating remotely when facility access is restricted?
- Where should we adjust systems to reduce downtime and optimise efficiency and throughput?
- What can we do to become more resilient and immune to global disruptions in the future?
We’re in this together
Collaboration during crisis helps us all weather the storm. This guide gives practical steps you can take right now to increase resiliency and agility. If you need help, we are ready to share best practices, experiences, and tools and techniques to rise to these unprecedented challenges together.
Tip 1: Protect health and safety
We know your first concern is to secure the health and safety of your employees and customers. While your workforce is scrambling to react to dynamic conditions, you’ll need to continually assess and respond to changes in health and government authority rules and guidelines.
Tip 2: Remotely manage operations
Take advantage of remote management software solutions trial periods so your operators can continue to adjust processes, conduct maintenance and make operational decisions to drive efficiency even when access to the physical plant is restricted or not desired.
Tip 3: Empower your workforce
Join Schneider Electric Exchange to learn and share best practices with your food and beverage peers and industry experts. Empower your workforce to make fast, informed decisions with digital technologies that put real-time plant operating information in a form they can readily use to improve productivity and operational profitability.
Tip 4: Practise good cybersecurity hygiene
Unfortunately, would be cyber-attackers ramp up activity in times of crisis. Food safety and cleaning processes continue to be cyber-targets for disruption. Conduct a comprehensive cybersecurity assessment and analysis and visit the Schneider Electric Cybersecurity Virtual Academy to learn what you can do to secure your operations.
Tip 5: Deploy OEE quick wins
Now more than ever, you need to make sure assets are always available for production when needed, avoid unplanned downtime, and use maintenance resources efficiently. Asset management solutions and modernisation services can improve the overall equipment effectiveness (OEE) of your plant and extend asset lifecycles. Analytics, which can be installed without stopping the plant, increase OEE, reduce operating costs, and shorten the time required for maintenance operations.
Tip 6: Improve agility
As market dynamics and consumer behaviour undergo drastic changes, you may need to adjust your product mix to accommodate shifts in demand. You may even have to suspend normal production in favour of making high-demand essential products. Use recipe and batch management to improve agility and reduce set up and changeover time. Digitising formula management and recipe execution can help you successfully manage flexible, multi-stream and multi-production operations.
Tip 7: Safeguard profitability
To offset revenue loss, look for places to reduce energy consumption, waste, and labour costs. You’ll need to understand the intricacies of your operations like never before to eke out every bit of production efficiency while you also streamline maintenance efforts. This will protect cash flow for financial continuity and resilience so you can positively impact profitability when economic and world conditions return to more predictable levels.
Tip 8: Increase supply chain flexibility and visibility
New digital technologies are available to help your supply chain more easily pivot to where it’s needed. If you don’t have it already, now is the time to look at end-to-end traceability and transparency across your supply chain. Transparency ensures full visibility on all information related to a product, proving their origin and highlighting information about ingredients, allergens, physical characteristics and other key attributes.
Tip 9: Future-proof operations to increase resiliency and agility
If these recent events have exposed problems — aging equipment, outdated processes, lack of digital talent, the need for real-time data to increase flexibility and make better decisions — the good news is that it has also uncovered opportunities. Create a prioritised list of where you need to make automation and digitisation improvements to become future-ready. We see digitisation as the path forward for F&B manufacturers to better align with modern customer needs and expectations.
To learn more, visit https://www.se.com/au/en/work/solutions/for-business/food-and-beverage.
Enhancing product safety and quality control with METTLER TOLEDO's inspection solutions
In the world of food manufacturing, ensuring the safety and quality of every product that reaches...
OD200: New Compact Distance Sensor Raising the Bar in Performance and Reliability
Launching in June 2025 from SICK’s HQ in Waldkirch, the new OD200 miniature distance sensor...
Heat and Control expands thermal range with Tek-Dry acquisition
Earlier this year, Heat and Control announced the acquisition of UK-based company Tek-Dry Systems...