The smart mill data for constant optimisation
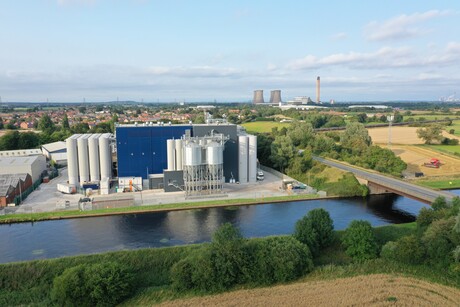
High-tech milling technology has been used to bring technological upheaval to Whitworth Bros., one of the UK’s largest millers. After a long and ongoing relationship, Bühler worked with the milling company to introduce its Mill E3 technology. The result is an energy-efficient, data-driven mill that is optimised around the constantly changing needs of its client.
The cost of the mill was reduced with the use of fast and easy-to-install equipment, which also kept the mill’s volume low. Its layout was designed with performance and reliability in mind and its equipment can easily be accessed for maintenance. The equipment has also been designed to ensure the safety of the milled products.
The mill takes a data-driven approach so it can constantly monitor and assess its own needs. Sensors through the various stages of milling are able to communicate with a central hub, feeding in information that can be utilised for optimisation. The equipment can adapt to changing conditions. For instance, the grinding system controls the distribution of feed depending on the exact properties of the wheat being fed into it. Sensors around the mill also push data to an online platform that can algorithmically compare processing parameters to optimise efficiency and performance. The system analyses more than 15,000 data points across the production process in order to keep things running well. In the future, a blockchain-based system will be brought online so that clients of the mill can transparently and securely keep track of the products that they are involved in.
“What is most exciting about the technology is that it provides the operator with data in real time, which enables the miller to take key and well-informed decisions about the plant,” said Mike Peters, managing director of Whitworth Bros. “We feel at Whitworth Bros. that we are pioneering and what we need to understand through the 15,000 data points are the optimum machine parameters required to ensure the continued manufacturing of high-quality products using digital technologies. Once that is defined accurately you can then be more exact in the way you set up your mill process and further push your process capabilities”.
Phone: 03 9872 7900
Rockwell Automation PointMax I/O
Rockwell Automation has released PointMax I/O, a flexible remote input/output (I/O) system...
NORD Drivesystems NXD tupH surface treatment
The NXD tupH surface treatment has been developed by NORD to make aluminium as resistant as...
igus D1 motor control with certified PROFINET
The igus D1 motor control can now be integrated into higher-level control systems from Siemens,...