Tailor-made oil refining line, remotely installed
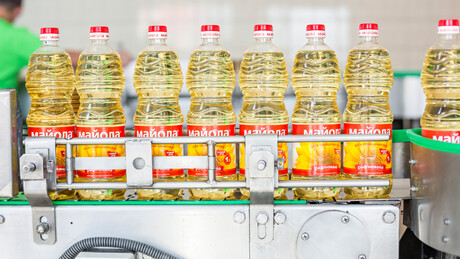
Edible oil producer Oliyar had ambitious goals.
The Ukrainian company wanted to improve oil quality, increase machine availability and process productivity, and reduce fixed costs while keeping their up-front investment low — all while dealing with a global pandemic.
GEA engineers came to the task and designed a tailor-made refining line remotely as border restrictions rendered travel impossible.
The engineers first had to identify an opportunity to improve on the standard process for refining edible oils. This usually involves two separate stages for water and special degumming. In this case, the process was condensed.
“GEA did not offer a simple standard solution, but instead designed the new refining process to our exact needs and specifications. As [a] result, we can now handle both water degumming and special degumming in one stage,” explained Taras Tsybuh, Production Manager at Oliyar.
GEA RSI separators feature GEA’s ‘finetuner’ technology, which allows for settings to be adjusted during processing to account for natural variation in oil compositions. Customers like Oliyar leverage this feature because it allows them to maximise yield while consistently meeting quality specifications. The finetuner also increases a plant’s flexibility, given a single separator can carry out all refining processes.
The integrated direct drive feature of the separators also eliminates the need for gears and belts. The company said this can deliver significant energy savings compared to gear-driven machines while reducing maintenance and downtime.
To ensure on-time delivery, the German team set up an intensive training schedule for their Ukrainian colleagues via videoconferencing.
“We guided the Ukrainian team through the entire commissioning process so they could repeat it at the customer’s facility successfully,” Birger Horns, Deputy Head of Business Line Renewables at GEA, said.
“The results have exceeded our expectations, both in terms of throughput capacity and separation results — and even better than promised in the original KPIs,” Taras Tsybuh said.
Phone: 03 9439 4122
Rockwell Automation PointMax I/O
Rockwell Automation has released PointMax I/O, a flexible remote input/output (I/O) system...
NORD Drivesystems NXD tupH surface treatment
The NXD tupH surface treatment has been developed by NORD to make aluminium as resistant as...
igus D1 motor control with certified PROFINET
The igus D1 motor control can now be integrated into higher-level control systems from Siemens,...