Cheese exporter upgrades inspection system on its grated cheese lines
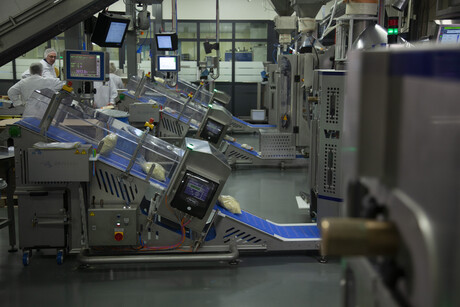
Dutch dairy company Vepo Cheese has streamlined safety and future-proofed its efficiency using Fortress Technology metal detectors. The company recently installed seven identical incline Interceptor metal detectors to overcome product effect on its grated cheese lines, all equipped with data reporting to enhance traceability.
Producing and packing millions of kilos of hard cheese annually, Vepo Cheese is well versed with automation efficiency. However, growing production demands prompted the company to examine further upgrades to its inspection technology, including the introduction of independent reject systems.
The increased sensitivity of the Fortress Technology Interceptor metal detectors was one of the primary reasons why the dairy processor selected seven to integrate with its vertical packing machines. The cheese maker specifically requested “inspection equipment that could deal with variations in density and product effect”.
The ability to isolate rejected packs without interrupting the production flow was equally crucial to Vepo Cheese.
On previous inspection lines, the company did not have an automated reject system. If a contaminated pack was identified, the belt would stop. An operative would then have to intervene to remove the pack and restart the inspection process, which impacted productivity.
“The automated reject system gives us 100% control over production. There is less human involvement, therefore less risk of human error. This also lowers the risk of a metal contaminant slipping through the safety net. From an efficiency perspective, continuous production is one of the main benefits,” said Vepo‘s Technical Operations Manager Hugo van Put.
Solving the conductivity challenge
Conductivity in cheeses generates product effect, impacting metal detection sensitivity. Previously, manufacturers of ‘wet’ products often had little choice but to tune their metal detection in a way that reduced margins of error. This tended to trigger excessive numbers of false positive rejects.
Tim Whyte, general manager of Fortress Technology New Zealand said: “Inspecting wet products has for many years presented dairy processors with several challenges. Due to the high moisture content, combined with minerals and salt, cheese like metal can be very conductive resulting in high levels of product effect.”
The Fortress Technology Interceptor software algorithms make it possible to adapt to these changing characteristics by distinguishing between indicators specific to the product and those that flag anomalies. It means that any genuine contamination from metal is not masked by product effect. AutoPhase is another useful tool from the company that can help to counteract product effect.
“These metal detectors are really sensitive,” van Put said. “This helps us to feel confident that the risks of contaminants are minimal, with less chance of a food safety issue. Having the double readings within the Interceptor system also lowers the risk of false-positive rejects, which saves on food waste.”
Digital data reporting
Processing transparency is another advantage of the fully integrated packing system. Each metal detector features Contact Reporter Software. Data from each packaging line is collated in a universal collection system, enabling quality assurance and production leaders to monitor processing and inspection performance from a centralised location.
The automated record keeper developed by Fortress Technology helps the dairy processor to keep track of and record data for rejects, tests and process settings. This has also helped to reduce maintenance and spare parts costs, according to van Put.
“As food processing plants get smarter, technology and digitalisation become even more imperative. Driven by ever-stricter safety regulations and the need for traceability across the supply chain, many processors are turning to inspection solutions with improved precision and greater digital capabilities,” Whyte said.
Critically for the dairy industry, the Interceptor can also be used to detect metal contaminants in free-flowing pumped dairy liquid or powdered product, Whyte said. Other valuable benefits include the ability to more accurately inspect product packaged in metal film.
van Put said: “We remain extremely satisfied with our new standards of quality assurance.”
Fortress Technology will be exhibiting at Foodtech Packtech 2025 from 2–4 September 2025 at Auckland Showground on Stand C16.
Phone: 0011 64 7 823 4111
Rockwell Automation PointMax I/O
Rockwell Automation has released PointMax I/O, a flexible remote input/output (I/O) system...
NORD Drivesystems NXD tupH surface treatment
The NXD tupH surface treatment has been developed by NORD to make aluminium as resistant as...
igus D1 motor control with certified PROFINET
The igus D1 motor control can now be integrated into higher-level control systems from Siemens,...