Automation system designed to guide bottles without breakage
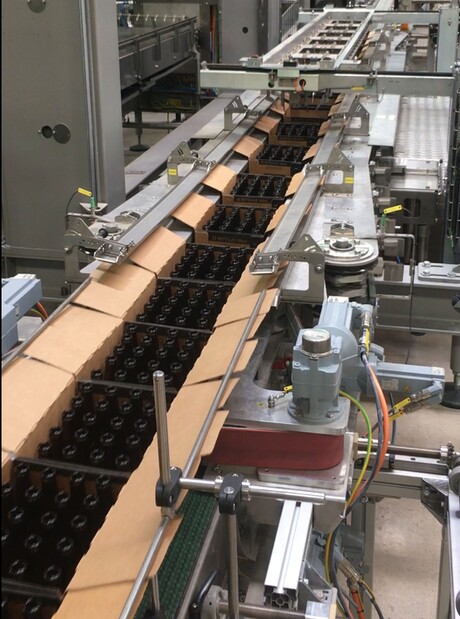
A large beverage producer in Mexico asked KHS to design an automated system for packing and unpacking bottles from its reusable cartons.
Most beverage bottles are transported in plastic crates as reusable cartons are less stable, which can cause difficulties during tightly synchronised transport automation and lead to broken bottles.
To enable the automated packers and unpackers to remove and insert the bottles from the cartons gently and precisely, the Dortmund-based system supplier faced the challenge of finding a guide system that could travel very small radii and right/left curves due to the limited installation space.
KHS worked with PGM Motion to develop a solution using its W-Line guideways integrated with specially developed guide carriages to negotiate the tight curves without breaking bottles.
“Cardboard boxes are much more unstable than plastic crates and so are already quite worn by the time they reach our production process. The difficulty now was to ‘divide’ these cartons in a way that was gentle on the product so that our packing system could insert or remove the bottles,” said Stefan Habermann, Head of Design – Product Centre Palletizing Technology at KHS.
“It is essential for the individual cartons to be positioned correctly on the pack conveyor so that the containers do not break and the conveyor belts rarely need readjustment.”
Carriages using traditional roller guideways have to be individually adjusted to the rails using eccentric bolts, and they are not able to travel on small radii with right and left curves without movement or load resistance. The transitions at the joints of the guide rails often have to be reground with an oil stone, which is time-consuming. These systems were therefore not feasible in this application.
PGM developed a solution that was specially designed for this application, based on a new design for the guide carriages and rail elements.
“The crucial advantage of this solution lies in the introduction of a spring package that permanently presses the carriages onto the rail using pre-tension,” said Joachim Öchsner, Managing Director at PGM Motion.
In contrast to conventional systems, where the movement increases over time and the carriages start to wobble, the movement of the PGM solution is designed to remain stable in the long term. The guide carriage rollers are in permanent contact with the rail, both in straight sections and in changing curve radii. There is no need to set eccentric bolts; the carriages are immediately ready for operation and can be replaced.
The cartons must be positioned precisely so that the packer and unpacker can lift and lower the bottles. The drive chain was therefore also adapted. A spring system enables the chain to elongate in the spring links, yet it remains robust enough not to be damaged by glass or shards.
A keyway is integrated at the ends of the guide rails to ensure good transitions between the rail elements, eliminating the need for manual reworking. Individual rail segments can be replaced as required.
Also, a permanent lubrication system is designed to prevent the carriages from wearing out over time, continuously delivering grease to the carriages.
Phone: 03 9335 1211
Rockwell Automation PointMax I/O
Rockwell Automation has released PointMax I/O, a flexible remote input/output (I/O) system...
NORD Drivesystems NXD tupH surface treatment
The NXD tupH surface treatment has been developed by NORD to make aluminium as resistant as...
igus D1 motor control with certified PROFINET
The igus D1 motor control can now be integrated into higher-level control systems from Siemens,...