A matter of time
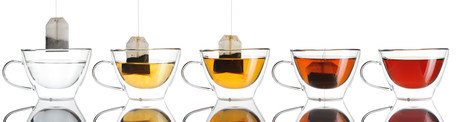
A Unilever-owned factory in Poland is 3D printing replacement parts for its equipment and making significant savings of time and cost in the process.
Katowice Beverages and Foods Factory in Poland is responsible for producing hundreds to thousands of bags of Lipton Tea every day. Thousands upon thousands of products are made, labelled, checked and shipped out nonstop with automated machines and sensing systems dominating the factory. Mateusz Loska is the professional maintenance specialist charged with improving the production efficiency of the factory’s systems — including anything from extending machine life to speeding up machine processes — all to save money and improve the machines at the same time.
At factories like this, quick turnaround time is essential to keeping machines running. The incentive of new ideas is driven by the promise of higher production rates, both in quantity and quality.
“We need to improve our machines in very short amounts of time,” Loska said.
“Sometimes there are parts that aren’t working... we used to just model the part, send it to a third-party company and wait for the results. It costs us time and money to fix a part. We’ve decided that we wanted to make this process shorter to make some improvements.”
Also if a new idea needs to be tested, it can take weeks to get the parts back from a machine shop. This was one of the processes Loska wanted to improve.
Cost* | Time | |
Replacement Part | $51.13 | 1 week |
Printed on Markforged | $23.01 | 1 day |
Priming for production
The factory had started with an ABS 3D printer at first, but it hadn’t quite lived up to their expectations: “We decided that we needed something more, that would produce parts stronger, that we could use during normal production, not just in testing,” Loska explained.
After hearing about Markforged, Loska was convinced: “We decided to test it... we saw that we could make models very quickly with the 3D printer, get stronger parts; not only with fibre materials like fibreglass or carbon fibre, but even with just nylon, we get much stronger parts.”
The prospect of a 3D printer that could create production quality parts was appealing to the entire team: “We realised this would save a lot of time for us... and everyone who was involved in this kind of work with our machines can see that 3D printing just makes the time shorter for developing new parts or new ideas through to production.” The Markforged printer gave the factory the ability to produce production prototypes at the push of a button.
Top of the line
When Loska and his team find potential areas for process improvements, they can now go straight to their Markforged 3D printer. “We start looking for any ideas, and during this process all the time we are 3D printing parts,” Loska explained.
Once they discover which part of their manufacturing set-up requires improvements, they can use the printer to not only prototype ideas, but to test and load their concepts in a real-world environment before finalising, and printing, the finished product.
With the capabilities of Markforged, the printer helps develop quality parts in a fraction of the time it would take otherwise.
From sensor mounts to new production ideas, Loska improved many factory processes using Unilever’s Markforged printer. Instead of waiting for weeks for a part to come in, this process now takes only a single day. “We make the 3D model in our CAD program, we send it to a third-party company... it’s about one week until we get back a good part,” he explained. “When we want to develop this part by ourselves, it takes 24 hours.
“These parts are developed very quickly, and it’s about one night to print a few parts for the machine. They are much stronger and more durable than any parts printed on a normal 3D printer.”
The parts the printer has produced can hold up in a factory environment, and that isn’t the only benefit: “Normally it’d be about $50 if we want to send it to another company to make it for us,” Loska said. “The same part costs about $10 on the 3D printer.”
Saving cost and time, the part strength Markforged provides has extensively improved production efficiency at the company: “These parts are developed very quickly, and it’s about one night to print a few parts for the machine. They are much stronger and more durable than any parts printed on a normal 3D printer.
Markforged’s 3D printing systems are capable of automatically reinforcing engineering plastics to aluminium levels of performance and beyond so businesses can easily manufacture parts with structural strength right on the desktop. The Mark Two Industrial Strength 3D Printer empowers professional users to affordably create workhorse 3D parts that solve real problems, as well as realise reinforced structures never before possible.
Markforged is represented in Australia by Emona Instruments Pty Ltd.
Phone: 02 9519 3933
Rockwell Automation PointMax I/O
Rockwell Automation has released PointMax I/O, a flexible remote input/output (I/O) system...
NORD Drivesystems NXD tupH surface treatment
The NXD tupH surface treatment has been developed by NORD to make aluminium as resistant as...
igus D1 motor control with certified PROFINET
The igus D1 motor control can now be integrated into higher-level control systems from Siemens,...