New! Instant Palletiser from Foodmach stacks 18kg on two pallets at 10.5 cycles/min
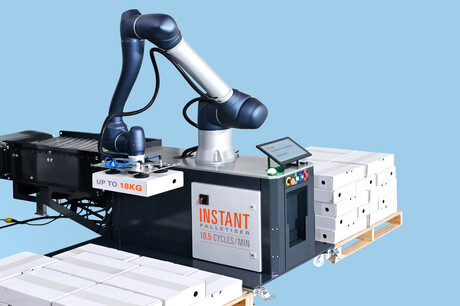
When it comes to palletising, there’s not a lot on offer for smaller manufacturers.
Automated palletising is an excellent way to get around labour supply and occupational health and safety issues while improving output and quality control. However, it’s expensive, requires a fair bit of conveying and floor space, and — unless it comes with pallet programming software — is a real headache to introduce new products and pallet configurations.
Cobots or collaborative robots are smaller, safer robots with a lower payload, designed to work alongside humans. They’re ideal for repetitive tasks that require dexterity and flexibility and can be easily programmed.
Cobot palletising is a good alternative, but until now, lacked the features, speed and payload to be of real use to FMCG production facilities. SMEs often produce a large number of SKUs of relatively low volume and would benefit from a palletising solution that’s easy to move around and set up, according to what’s being produced. The perfect solution for smaller manufacturers would offer absolute flexibility, be easily deployed (plug and play) and take up about the same amount of space as manual palletising.
Enter the Instant Palletiser
Compact and mobile, a new cobot-powered palletiser, or ‘Instant Palletiser’, has just been launched in Australia by Foodmach’s Technology Products division. It requires little in the way of set-up and is simply wheeled into place and connected to air and 240v power. Once case and pallet sizes are entered on the 13″ interface, the built-in software does the rest. It requires zero programming, training, calibration or technical skills to operate. Nor does it require safety fencing.
Instant Palletiser has an effective maximum case payload of 18kg and stacks pallets up to 1,550 mm high at rates of up to 10.5 cycles per minute. An enhanced option allows stacking of 2,500 mm tall pallets at rates up to eight cycles per minute. A skewed conveyor ensures all incoming cases are aligned consistently for the cobot’s gripper. Inbuilt sensors confirm the pallets are in position. The entire footprint is 3,607 x 2,636 mm, including two pallets.
Continuous Operation
Instant Palletiser can stack at two pallet locations on either side of the base. The benefit of this is that an operator can remove a completed pallet while the cobot continues to palletise a secondary pallet without interruption. Or it can be configured to stack two different SKU’s to each pallet location simultaneously. A third option opens the opportunity of placing slip sheets between each pallet layer. Indicator lights communicate the status of each pallet to the operator, so there’s no confusion.
Flexibility
Different box or item surfaces can be handled by Instant Palletiser, which adapts to all object configurations and product size changes. The software allows an operator to define a box size using three dimensions and a pallet pattern, which is then translated automatically into the cobot program.
Safer Pallets
The smart software makes it easier to stack pallets with interlocking pallet patterns, making stable pallets less inclined to collapse. The software generates a range of pallet stacking pattern options, allowing the operator to choose the preferred pattern. It even ensures that case barcode labels are facing outwards, where required.
Safer for People
Physical safety is the key issue on any factory floor. Instant Palletiser has been fully risk-assessed to comply with all relevant Australian safety regulations. It comes fitted with five area scanners mounted in a vertical barrier pattern around the unit. When no human presence is detected, it operates at the maximum speed of 10.5 cycles per minute. If the safety zone is entered, the palletiser can be configured to stop entirely or continue operating at a suitably reduced speed, dependent on payload.
Grippers
Manual labour is restricted to what can be lifted safely. By changing the type of gripper on a robot — such as pads, fingers or suction cups — pretty much anything can be lifted without fear of dropping it. Instant Palletiser comes with a pneumatic or an electro-mechanical case gripper. A custom-designed vacuum gripper with two channels means two boxes can be picked simultaneously, increasing the palletising rate to 21 boxes/min if required or if total weight permits. The infeed conveyor gating system always ensures the correct flow of boxes to the pick station.
Rapid Deployment
Traditional palletisers require extensive planning and calculations to ensure they are fit for purpose (correct centre of mass for products, correct payloads and robot arm reach to maintain balance etc.). A smart cobot palletiser solution, managed by software, offers all these calculations on the fly. An online simulator can be used for layout and test purposes, and pallet/product configurations can be changed easily.
Instant Palletiser is moved into place on castor wheels, pallet trucks or a forklift. Short production lead times make it an attractive option for businesses needing a quick fix. It offers the only work cell that doesn’t need pick point programming because the integrated skewed conveyor ensures the incoming case is always in the same pick location.
Wrapping it up
For SMEs, cobot palletising will overcome current labour shortages, reduce risky repetitive tasks and labour hours at the end of the line and deliver a more consistently-stacked pallet. It supports overall efficiency and production rates, providing an edge many SMEs need.
Palletising made simple in 5 easy steps!
- Roll Instant Palletiser into place and connect it to power and air.
- Power up the unit.
- Enter case dimensions and weight and select pallet type.
- Let the automated pallet pattern generator create the stacking strategy.
- Start palletising!
About Foodmach Technology Products
Foodmach is best known for its award-winning palletising and pallet configuration software. Our Technology Products division is responsible for finding the world’s finest packaging technology to add to our portfolio. Instant Palletiser is the latest addition to our extensive range that comes with Foodmach service and support.
New Report Reveals Next-Gen Tech Driving Major Growth in Australian Food Processing
With the rise of AI-powered forecasting and automation, the timing is ripe for businesses to...
Racking Up Results: How Jimba Lamb Got Its Inventory in Shape
How a homegrown inventory solution helped United Meat Co's Australian arm, Jimba Lamb, gain...
PE20 Palletising System by Optima Robotics
Amid labour shortages, increasing expenses, and safety worries, businesses of all sizes are...