Global beverage manufacturer improves safety and performance
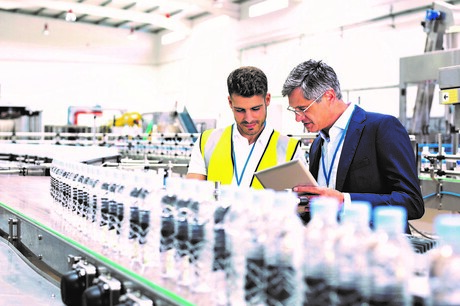
Depalletiser and infeed conveyor upgrade improves safety and reduces risk while optimising productivity.
Food and beverage processing is Australia’s largest manufacturing industry. From large multinational companies producing volume fast moving consumer goods, to small niche producers, the industry is diverse and growing.
In today’s market, food and beverage manufacturers are continually challenged to streamline their processes to reduce downtime and improve productivity and performance. To maintain their competitive edge, they need to be more flexible and agile to cater for constantly changing consumer preferences.
Food and beverage manufacturers need to have safe and reliable production processes that consistently deliver high quality products, each time. They have a moral and regulatory obligation to safeguard their workers while maintaining productivity and business performance.
The Australian manufacturing industry is identified as a national priority to reduce the number and rates of fatalities and serious claims in the Australian Work Health and Safety Strategy 2012-2022. The industry has the second highest serious claim frequency rate with 8.9 serious claims per million hours worked. However, the rate has decreased by 38 per cent over the past decade which is likely a result of improved safety standards and compliance.
From conveyor processes to high speed filling and packaging, there are several processes in a beverage manufacturing plant where safety is paramount. In fact, a recent Manufacturing Industry report by Safe Work Australia stated that 18 per cent of injury claims are a result of muscular stress while lifting, carrying, or putting down objects. This highlights the importance of limiting manual handling where possible through automated palletising.
The challenge for many companies is to meet safety goals while achieving high availability and asset utilisation. This was a key priority for a large, global beverage manufacturer who recently conducted a safety upgrade project on their conveyor and depalletizing machine lines. With a strong commitment to safety, the manufacturer knew that by reducing safety risks and improving compliance, they could optimise their asset productivity.
Pilz was chosen for the turnkey project since it demonstrated high expertise, skills, capacity, and confidence to deliver the project within a short time span to meet the customer’s schedule.
Assessing the risk
Often just a few factors can lead to an accident, making risk assessments key to machine safety. The first step to machine safety, the risk assessment aims to determine and assess existing hazards and to define measures for risk reduction that are both effective and economical.
“The scope of this project required a risk assessment in accordance with AS/NZ 4024.1201 to assess the infeed conveyors as well as the depalletiser at the plant. Our methodology approach included risk analysis, hazard identification, risk estimation and evaluation,” said Raju Subramani, Project Manager, Pilz.
Upon presentation of the risk assessment, Pilz was asked to implement the safety system and upgrade the machines to mitigate the risks identified. This involved a turnkey project including, an electrical design safety upgrade, mechanical safety guarding upgrade, trapped key system, and validation of the safety system.
From concept to design
Developing an effective safety concept was key to addressing the safety requirements identified in the risk assessment. Pilz worked closely with the manufacturer to develop the safety concept and design so that implementation costs, interaction between operator and machine, productivity and asset utilisation were optimised.
Through the safety design process, Pilz was able to address risks through detailed planning of the necessary safeguards plus the selection of appropriate technologies. By integrating a detailed safety design before the concrete implementation, it was possible to increase the machine’s availability, as well as reduce downtime to a minimum — a key priority for manufacturers.
Due to the high-speed conveyors and palletisers, the plant required a control system with high level functional safety. The PNOZmulti controller provided an easy to configure control solution with multiple safety functions to meet the machine requirements. With additional safety I/Os and safety switches and locks, the safety upgrade was able to keep workers safe from potentially hazardous machine movements.
Pilz also provided the construction and erection of the required mechanical structures as well as the assembly and testing of electrical panels. Axelent Australia, a Pilz authorised System Partner, delivered the machine guarding to meet the machine’s safety guarding requirements and keep workers safe during production.
Plant safety was provided through the latest mechanical, technical and organisational measures, to reduce risk and maximise productivity.
Validating the system
Once the system was commissioned and installed, it was validated against the safety requirement specification. Pilz conducted a function test and fault simulation on the safety system and tested the technology to ensure it was working effectively and that all safety requirements were validated in accordance with the applicable regulations and standards.
This provided reassurance to the manufacturer that their safety and performance requirements were fulfilled to the highest standards. It also ensured that the system was implemented seamlessly while demonstrating compliance to safety standards.
Safety success
Being a large global beverage manufacturer, asset utilisation and productivity was critical. Pilz worked with the manufacturer to ensure that the project was conducted within a short time span with limited interruption to production.
Thanks to experienced project management and local service and support, Pilz was able to deliver the upgrade within the plant’s planned shutdown period — avoiding any unnecessary impact on production. The plant can now benefit from improved safety, reliability and asset utilisation helping to meet growing consumer demand.
The safety implementation has met the requirements to comply with the local regulation, international and Australian standards together with the manufacturer’s own high standards for quality, reliability and safety.
New Report Reveals Next-Gen Tech Driving Major Growth in Australian Food Processing
With the rise of AI-powered forecasting and automation, the timing is ripe for businesses to...
Racking Up Results: How Jimba Lamb Got Its Inventory in Shape
How a homegrown inventory solution helped United Meat Co's Australian arm, Jimba Lamb, gain...
PE20 Palletising System by Optima Robotics
Amid labour shortages, increasing expenses, and safety worries, businesses of all sizes are...