Choosing compressed air for food and beverage sectors
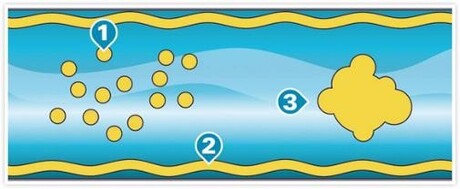
What type of compressed air should food and beverage manufacturers use?
The short answer is “Best possible quality”. The full answer is a bit more complex to explain…
If only there was a way to quantify compressed air quality and express the various levels of the quality in easy-to-understand terms. Easy! The International Standards Organisation has derived a simple framework to define compressed air quality using a quality class system. Known as “ISO 8573-1 Compressed Air – Part 1: Contaminates and purity classes”, this Standard has been used for decades and is a very handy reference document for specifying and verifying compressed air quality.
ISO 8573-1 specifies purity classes of compressed air with respect to:
- Particles (dust)
- Water (moisture)
- Total Oil (liquid, aerosols and vapour)
For each of these contaminate types, the ISO standard sets quantifiable levels and assigns each level to a number. The lower the number, the better the quality level of the compressed air.
But what quality of compressed air should be used to make food and beverages?
Let’s break it down to each potential contaminate, particles, water and total oil.
Particles
Particles can include sand, salt, sugar, black carbon, rust, cement, paint particles, skin flakes, and more important good food hygiene, spores, bacteria and even viruses.
This is the easiest contaminate to deal with and can be solved with simple but effective dust filters. Some F&B industry specific “best practice guideline” recommends ISO 8573-1 Class 2 for dust, Atlas Copco recommends Class 1 instead. Most microorganisms will pass through Class 2 filters but will be effectively trapped by Class 1 filter sets. Dust filters are the lowest cost of all compressed air quality equipment costs so specifying Class 1 instead of Class 2 can reduce particulate count in compressed air by a factor of 20.
Water
Water is naturally present in the atmosphere and so will also be present in compressed air. In most applications, compressed air is dried to reduce the chance of condensation in pipework and pneumatic devices. Compressed air with a Relative Humidity (RH) of less than 25% will eliminate condensation in compressed air systems which will prevent rust and prolong the life of pneumatic devices such as air motors, cylinders, actuators etc. This level of dryness can be achieved with refrigerated dryers resulting in ISO 8573-1 Class 4 for water. However, food and beverage applications generally need higher level of dryness to ensure food hygiene and safety. This is because air can contain microorganisms (bacteria, fungi etc.) which grow and multiply in the presence of moisture and nutrients.
Compressed air with a RH less than 20% is considered food and hygiene safe. The below table shows the relationship between ambient temperature and pressure dew point (PDP) at various RH.
As can be seen in the table, a PDP of -20°C avoids growth of microorganisms in compressed air.
Atlas Copco recommends ISO 8573-1 Class 3 for water. This corresponds to a PDP of -20°C or less and will generally deliver compressed air with a relative humidity less than 10%, well below the dryness level needed to protect food safety and avoiding hygiene hazardous. Coupled with ISO 8573-1 Class 1 for particles which reduces microorganism count in compressed air by a factor of 20, Class 3 for water will inhibit growth of all living particles in compressed air.
Total Oil
Whereas particles and water are naturally found in atmospheric air, oil is not. ISO 8573-1 defines total oil in compressed air as the mixture of oil aerosols, liquid oil and oil vapour.
Forms of oil contamination in compressed air pipework:
- Aerosols (liquid oil suspended in air)
- Liquid Oil (which can flow along the inside walls of compressed air pipe)
- Vapor
According to the ISO standard, all forms of the oil are defined as a mixture of hydrocarbons with 6 or more carbon atoms (C6+). These complex hydrocarbons are typically found in lubricating oil. So all oils are hydrocarbons but not all hydrocarbons are oil.
As a contaminate in compressed air, oil is the most difficult to manage. In a typical compressed air system with an oil-flooded air compressor (also called oil-lubricated or oil-injected), a system of up to 5 separate oil reducing stages are needed to minimise the degree of oil contamination in the compressed air.
5 Separate Stages of Oil Reduction used in typical oil-flooded compressor system
Each of these stages has to operate perfectly to guarantee the oil content of the compressed air. If the operating conditions of any of these stages are exceeded or if they fail, the entire system will be overwhelmed, leading to high degree of oil contamination of every food and beverage product in contact with compressed air.
To further complicate this process, oil concentration in compressed air is exponentially related to compressed air temperature. The performance of separators, coalescing filters, dryers and active carbon filters used in a typical oil-reducing system are generally specified at a compressed air temperature of 25°C. The oil-content can be up to 20 times higher when the compressed air is 45°C. Given that the temperature of compressed air is generally 10°C higher than ambient air temperature at the filtering stage, these oil reducing stages could be overwhelmed when the ambient air temperature reaches just 35°C.
Atlas Copco recommends ISO 8573-1 Class 0 for total oil. Oil does not have to be used in the compression process and there are many technologies available that produce oil-free compressed air. Such compressors can be independently tested and certified as Class 0 using the test methods recommended in various parts of ISO 8573 Standard even up to ambient air temperature of up to 50°C. No need for separators, coalescing filters and active carbon filters to manage oil contamination!
Conclusion
The best possible quality of compressed air for use in food and beverage applications is ISO 8573-1 Quality Class 1.3.0. This air quality class provides the best protection against contamination from particles (including microorganisms), water (to ensure food hygiene safety) and zero risk of any oil contamination.
To find out more, you are welcome to contact our food and beverage compressed air specialists. Find out how by visiting https://www.atlascopco.com/en-au/compressors/industry-solutions/food-beverage.
New Report Reveals Next-Gen Tech Driving Major Growth in Australian Food Processing
With the rise of AI-powered forecasting and automation, the timing is ripe for businesses to...
Racking Up Results: How Jimba Lamb Got Its Inventory in Shape
How a homegrown inventory solution helped United Meat Co's Australian arm, Jimba Lamb, gain...
PE20 Palletising System by Optima Robotics
Amid labour shortages, increasing expenses, and safety worries, businesses of all sizes are...