Overcoming challenges experienced with sleeved grate magnets
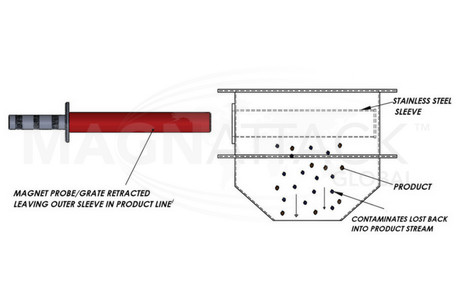
In the past, stainless steel sleeves on the outside of magnet grates, drawers and cartridges were commonly used by the food industry. Today, while still utilised in some food processing operations, many industry professionals do not perceive them as being as sanitary or as effective as other grate magnet designs — despite their easy-cleaning operation.
An increased concern for food safety and sanitary systems means that sleeved grate magnets are somewhat a concern and can possibly have a negative effect on foreign metal fragment control. This highlights these concerns and provides alternative magnetic separation solutions — but first, it is important to understand how stainless steel sleeves work.
What are magnet sleeves?
Magnet sleeves are thin stainless steel covers that are positioned over magnet bars for drawer and grate systems that are in contact with a product flow. Magnet sleeves are typical of old-style grate-in-housings or drawer magnet systems. The magnet is inserted into the stainless steel sleeves, meaning that collected metal contaminants are retained to the outside of the sleeve, not to the magnet rod itself.
In an attempt to create a more efficient and simple cleaning process, magnetic separator manufacturers introduced the sleeved grate magnet design — and in effect, it works. To clean a sleeved grate magnet, all plant operators must do is remove the sleeve and magnet assembly from the housing, then pull the magnet out from inside of the sleeves… and just like that, the collected metal fragments drop off!
Manufacturers and suppliers of the sleeve design would market benefits such as these:
- Rapid and effortless cleaning — with no wiping or brushing required.
- Minimal product loss.
- Protection of magnet bars from abrasive wear.
- These features would be very attractive to plant operators and seemingly provide an answer to troubles associated with cleaning magnets.
So why are magnet sleeves troublesome?
Disadvantages associated with sleeved grate magnets
Regardless of these ‘benefits’, sleeved magnets inherently carry several problems. Some of the most prevalent consist of:
- Unhygienic design.
- High risk of recontamination.
- Loss of magnet retention.
- Prone to wear and damage.
- Jamming.
Unhygienic design
Magnet sleeves are a breeding ground for bugs and bacteria. Food product (or any type of contaminant for that matter) that is entrapped between the sleeve and the internal magnet can trigger mould and bacterial growth. This is a serious sanitary concern and the justification for sleeved magnet configurations being excluded from the HACCP International Food Safety Magnet Standard 0909MAGSEP 1-2010.
High risk of recontamination
There is a high risk that collected metal fragments may recontaminate the product if the magnet sleeve assembly is not fully removed from the product stream before cleaning is initiated. In addition, some poor designs of these systems allow for the magnets to be extracted from the sleeves while the assembly remains positioned in the flow of product.
This presents a highly dangerous risk (and almost certain chance) of captured metal fragments being discharged back into the product.
Loss of magnet retention
As explained earlier, sleeves are positioned between the product flow and the magnet bars. Regardless of how thin the sleeves are, they still have a negative effect on the surface strength of the magnet, and therefore impact on the magnet’s ability to retain weakly magnetic fragments.
Prone to wear and damage
This is a concern in all applications, but especially those of abrasive nature such as grains and seeds. Sleeves are required to be very thin to allow for adequate magnet strength. Due to the fragility of thin sleeves, the likelihood of damage and wear is high. If the outer sleeve becomes damaged or dented, the inner magnet can become jammed, which can cause consequent wear to the inner magnet and create cleaning difficulties… again, leading to hygiene concerns.
Jamming
As mentioned in the previous point, the inner magnet can become stuck inside the sleeves. This can cause great difficulty during the cleaning process and create OSHA risks if operators attempt to forcefully pry apart the jammed assembly.
While in their time sleeved grate magnets were a revolution to ease cleaning of magnets, they are now considered outdated in most food applications due to food safety concerns, OSHA and other important considerations.
So what magnetic separator designs are an advancement on sleeved grate magnets, and why?
Overcoming problems associated with sleeved grate magnets
While the sleeves satisfied the industry’s desire for an easier cleaning process, they created several questions and difficulties. Food processors would ask:
- How can we keep our magnets sanitary?
- How can we reduce the risk of recontamination?
- How can we prevent sleeves from jamming?
With food safety being a top concern, the need for easy-cleaning magnets evolved into the need for easy-cleaning magnets that are sanitary, robust and hold minimal risk of recontaminating the product stream.
One response to this need is the RE80 RAPIDCLEAN Easy-Clean Grate Magnet.
Why?
- Swing-out or swing-away design means cleaning is performed wholly outside of the product area — collected fragments fall into a tray rather than back into the product stream. The RAPIDCLEAN Grate Magnet cannot be cleaned while in the product stream.
- The food product is in direct contact with the magnet bars — in addition to presenting higher magnet retention strength, this also eliminates the risk of bacterial contamination forming between the magnet and the sleeve.
- No internal ledges or supports — once again, a common hiding place for product build-up, bacteria and mould is removed.
- Single bar cleaning method — eliminates the risk of drawer jamming, and the consequence of magnets not being able to be cleaned properly.
- DURA-SLIK abrasion resistance — patented technology to shield against damage and wear caused by abrasive products.
Self-cleaning MAG-RAM grate magnets are also favoured in the food industry as an alternative to conventional grate magnets. The automatic cleaning process removes the need for manual human operation.
- No risk of human ingress to the product stream (which may cause bacterial contamination).
- Elimination of OHS/WHS issues experienced with lifting heavy grates for cleaning.
- Unique DURA-SLIK abrasion reduction technology equalises abrasive wear on the surface of the magnet.
- Elimination of metal fragment issues caused by operator error during cleaning.
- No need for operator cleaning schedules as automatic cleaning can be performed before, during and after production runs.
With the development of grate magnet systems, such as the RAPIDCLEAN and MAG-RAM, the food industry can be assured of the highest level of metal contamination risk reduction without risking important sanitary and food safety considerations.
As with all MAGNATTACK equipment, the RAPIDCLEAN and MAG-RAM are certified by HACCP International and conform to current industry food safety standards.
Phone: 02 4272 5527
Key Technology COMPASS Belt-Fed Optical Sorters
Key Technology introduces the COMPASS belt-fed optical sorters.
Olivo multi-temperature food transport solution
CoolPac has introduced Olivo insulated food containers, which are designed for the transportation...