Macadamia processor cracks into the latest sorting tech
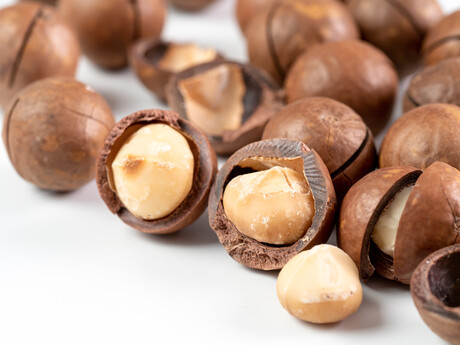
When a group of South African macadamia farmers decided 20 years ago to collaborate in processing and marketing their crops themselves, they initiated a strategy that would prove successful.
Anticipating the need to produce macadamias in even greater quantities while ensuring quality, Golden Macadamias is expanding its factory near Johannesburg with the goal to be operational in the 2022 season.
The company has invested in the TOMRA 5C premium optical sorting machine, which has been explicitly developed for nut and dried fruit applications. When this machine is combined with TOMRA’s unique Biometric Signature Identification (BSI) scanning technology, it can also be used to detect and eject product defects.
Macadamias are still seen as a young industry and comprise about 1–2% of the total world tree nut basket, with almonds, walnuts, pistachios, cashews and hazelnuts contributing 95%.
Norman Smith, Area Sales Manager Africa, TOMRA Food, said: “Today 98% of the macadamia crop is exported. Approximately 55% of South Africa’s macadamias are sold to the kernel market, mostly for export to the USA, Europe and Asia. The other 45% goes to the in-shell market, some for sale domestically but mostly for export to China, where consumers prefer to crack the shells themselves. It is the kernel market which demands the greatest product quality.”
A mix of manual and automated sorting
Macadamia nuts are harvested after they have fallen naturally to the ground. The first task is to remove the green outer husks, then the nuts in their shells are sorted to remove foreign materials and defective products. After this, the nuts are graded by size. Because two-thirds of each nut comprises shell, processors have to deal with an extremely high defect level after cracking the nuts.
Significant quantities of shell must be moved removed to clean up the kernel. Some macadamia sorting is still done the traditional way, by hand. In addition to grading being done manually, nuts are put into a water bath early in the production process, where only the unwanted immature and underdeveloped nuts float to the surface and can be manually removed. But human sorters are unavoidably subjective, imperfect and more vulnerable to error when tired or bored.
Manual sorting can also diminish product quality because handling kernels makes them oilier. To minimise these drawbacks, Golden Macadamias complements the sorting tasks that have to be done manually with sorting wherever possible by machines. Unlike human beings, automated sorters can assess nuts objectively, accurately, consistently and at speed for hour after hour without any deterioration in efficiency. What’s more, mechanical sorters can detect and eject a vast range of in-shell defects invisible to the human eye. Product quality is enhanced through these automated capabilities, throughput is high, food waste minimised and yield improved.
Golden Macadamias employs TOMRA’s BSI technology after the nuts are cracked and before they are manually graded.
Peter Edmondson, General Manager at Golden Macadamias, commented: “Our partnership with TOMRA has proved strong throughout the years. It has allowed us to pioneer the ideal processing solution for the macadamias market, where we continuously develop new solutions and technologies.”
The TOMRA 3C eliminates foreign materials, including stones, shells and sticks, and, depending on the sorting process, can achieve an efficiency of up to 99.5% purity. It is also suited to separating shell from kernel with a low giveaway. The machine is capable of sorting more than 20 tons of nuts per hour.
The TOMRA 3C can also be used in a second position on the line to remove major discolorations, rotten and mouldy kernel, and any remaining shell. The TOMRA BSI+ technology can then scan materials with both near-infrared (NIR) and visible spectrum wavelengths. This instantly compares the biometric characteristics of objects to features stored in its database to determine whether they should be accepted or rejected.
Edmondson said: “As well as identifying the hard-to-find defects, TOMRA’s BSI technology has increased factory throughput by 10%. This means the payback period for the technology will be no longer than about two years.”
These results convinced Golden Macadamias to purchase the recently launched successor to the Nimbus, the TOMRA 5C, the latest platform to use BSI+ Technology.
Phone: 02 8624 0100
Key Technology COMPASS Belt-Fed Optical Sorters
Key Technology introduces the COMPASS belt-fed optical sorters.
Olivo multi-temperature food transport solution
CoolPac has introduced Olivo insulated food containers, which are designed for the transportation...