Oil-free air and lower energy costs for dairy processor
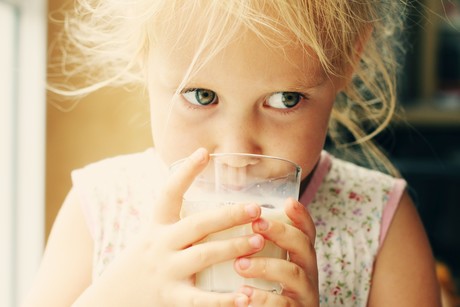
Hochwald Erfstadt dairy in Germany is a rapidly growing site, with continuous investment in production needed to keep pace with consumer demand for a wider range of products, including fresh and long-life milk, cheese and yoghurt.
High quality and safety standards
Compressed air is used at many points in the production process, such as when emptying tanks and during sterile filling, placing stringent requirements on its quality.
In order to achieve these standards, the Erfstadt factory operates two compressed air networks: one produces oil-free air for the central processing stages and a second, smaller network uses oil-lubricated compressors to supply the packaging machines, where the air does not come into direct contact with the product.
Producing oil-free compressed air
Until recently the compressor station housed four CompAir piston compressors, which supplied around 68 m3/min of compressed air to the oil-free, 8-bar network. To optimise energy usage, Hochwald technicians developed a practical, demand-based control system for the four compressors. The machines are regulated at half load and controlled centrally, producing eight power levels which fit the demand profiles perfectly.
Choosing Quantima
When Hochwald started considering the expansion of the compressed air station, it seemed obvious to install two further piston compressors in the space available. However, CompAir proposed a system comprising one new Quantima unit.
Compared to a conventional compressor of the same performance class, a Quantima compressor has less than half the footprint. Hochwald elected to install one of Europe’s first Quantima Q-43s, with a 250 kW drive and maximum volumetric flow of 43 m3/min.
Using Quantima
As the largest machine in the station, the Quantima speed-regulated compressor handles the base load and, therefore, usually runs at full load. The piston machines are then activated in a cascade when the requirement exceeds 43 m3/min. A huge, 30 m3 storage tank ensures that peaks in load are buffered. Shortly after Quantima was installed, a volumetric flow-recording unit was fitted for all lines and departments. As the compressed-air-related power requirement is known, this is enabling Hochwald to calculate the compressed air costs with great accuracy.
Using Quantima in place of a standard compressor can cut energy use by up to 25%. The variable-speed drive matches air output automatically to plant demand to provide the precise volume of compressed air needed, helping to minimise off-load running. When idling at 2.5%, a Quantima compressor requires just a fraction of the energy needed by a screw or standard turbo compressor.
Compressor operations are monitored by the intelligent Q-Master control system, which continually records and checks all system parameters. The system also allows for remote analysis and diagnostics of compressor performance.
Plant manager Ralf Fuchs said, “We always monitor the return on investment for any new equipment we purchase and features such as reduced energy demands of course impact on payback. Factors like energy saving and the compact design tipped the scales when it came to making this investment.”
Phone: 03 9212 5800
Rockwell Automation PointMax I/O
Rockwell Automation has released PointMax I/O, a flexible remote input/output (I/O) system...
NORD Drivesystems NXD tupH surface treatment
The NXD tupH surface treatment has been developed by NORD to make aluminium as resistant as...
igus D1 motor control with certified PROFINET
The igus D1 motor control can now be integrated into higher-level control systems from Siemens,...