Crisp manufacturer doubles pack speed and reduces wastage
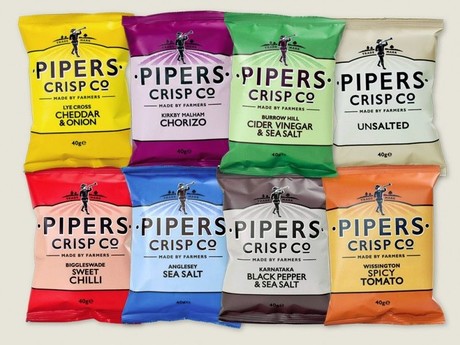
UK gourmet chips manufacturer Pipers Crisps has doubled its packaging capacity and reduced waste thanks to the installation of high-speed packaging solutions. The new installation has enabled Pipers Crisps to increase productivity, while maintaining the highest level of product quality through enhanced seal integrity.
Based in Brigg, Lincolnshire, the company was established in 2004 by three farmers who joined forces to produce great-tasting, quality chips using local potatoes. Today, its award-winning products, recognised nationally for their unique and bright packaging design, are distributed throughout the UK, as well as exported to Europe and the US. Following a period of impressive growth in the past two years and rising popularity of its products, Pipers Crisps needed to add new packaging lines to its existing packaging fleet to cope with the additional demand.
Meeting increased demand
With existing equipment achieving throughput speeds of only 80 bags per minute (bpm) for its smaller bags, Pipers Crisps needed to substantially increase bagging speed. The premium chips manufacturer opted for two tna robag FX 3ci vertical, form, fill and seal (VFFS) packaging solutions. These high-speed baggers feature a very short vertical product transfer from the scale to the pack, helping to maximise packaging performance. The new set-up allows Pipers Crisps to package a variety of bag sizes at speeds of up to 140 bpm, resulting in a 75% increase, in line with the company’s capacity uplift.
Catering for a variety of snacking occasions, the chips manufacturer needed a packaging solution that could switch between two different pack sizes — 40 and 150 g — of high-quality pillow bags, without lengthy changeover times that would slow down or even stop production. With its lightweight formers, unload assist and twin film spindle, the flexibility of the tna robag FX 3ci makes changeovers fast and easy, enabling operators to easily switch from one bag size to another on the same packaging line.
Assuring quality and seal integrity
The Pipers Crisps brand is renowned for its premium positioning. In such a highly competitive market, quality is crucial to help differentiate brands on retail shelves. It was therefore important that the chosen packaging solution could maintain seal integrity and reliably produce high-quality bags that do not compromise the shelf life of the product within it.
“During the packaging process, pieces of chips can get caught in the bag seal, compromising seal integrity and reducing the shelf life of the product. When this occurs, it can often lead to product rejects and waste,” explained Simon Hill, Regional Sales Manager at tna.
With its innovative rotary jaw design and advanced sealing technology that offers improved seal performance at high speeds, the tna robag FX 3ci proved to be the perfect solution. Featuring patented stripper tube closures, the completely integrated packaging system allows for better control of the product through the packaging and filling cycle, therefore helping to control dust generation and minimising crumbs in the end seal of the bag.
The tna robag FX 3ci was also customised with product-in-seal-detection (PISD) software that monitors product in the seal and jaw area. If seal integrity is compromised, the system immediately alerts the operator so that bags can be quickly removed from the line for further inspection. That way Pipers Crisps is able to ensure that each bag meets the highest quality standards while keeping waste to an absolute minimum.
Richard Mottram, Factory Manager at Pipers Crisps, commented: “Before the installation, we experienced 3% wastage at 80 bpm, as we had to manually detect and remove any bags with compromised end seals or pleats before they entered the packaging area. Now, our wastage is down to 1% at 140 bpm, which has surpassed our expectations. As a result, it has helped us gain better control over product losses and achieve operational cost savings, while contributing to quality assurance.”
Phone: 02 9714 2300
SIG recycle-ready, bag-in-box packaging for wine
SIG has partnered with Australian wine producers to produce a recycle-ready bag-in-box for wine.
BMT Blowscan and Thermoscan rPET bottle perfecting systems
Blowscan and Thermoscan are designed to help manufacturers improve PET bottle performance, reduce...
Henkel Loctite Liofol LA 7837/LA 6265 solvent-free adhesive system for packaging
The system is tailored for applications involving high thermal stresses — in particular...