Aseptic filling for Nectar
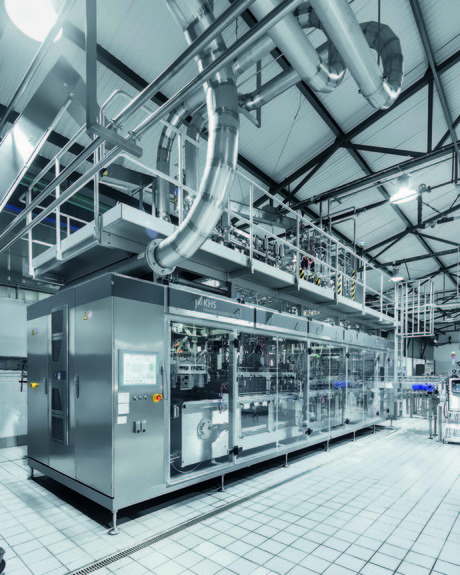
Serbian fruit juice producer Nectar covers all stages of the value chain: from its own plantations through purchasing, fruit processing and cooperation with fruit farmers to the finished product.
Until very recently the company pasteurised and filled sensitive products using ultraclean filling technology (UCF), where overpressure is applied to the filling and capping zone. The air is fed in through filters to prevent any possible microbiological contamination. In addition, the empty bottles are first filled with nitrogen to improve the microbiological quality of the filling process.
In order to satisfy its own growing demand for quality, Nectar has now opted for aseptic filling. This allows its range of products to be considerably expanded — both with regard to the fruit content and the various flavours and product variants in all categories.
“For us, the most important thing is that we can now carry out this process under sterile conditions,” said production manager Milka Tomanović. “This retains the natural properties of the fruit. We have a better quality of final product and can offer greater microbiological quality over a longer period.”
Creating sterile conditions for aseptic fillers is a tricky undertaking. It was thus soon clear to Nectar that the only technological partners to come into question were certified systems manufacturers proven worldwide.
Nectar had become convinced that the high standard it required for its own products could only be achieved by using equipment of an equally top quality. The company opted for an Innosept Asbofill ABF 711 C — the first aseptic filler of this kind for the production of fruit juice in Serbia.
The line has a capacity of 12,000 bottles/h and processes 500 mL, 750 mL and 1.5 L PET bottles. Nectar not only invested in a filler but also in a stretch blow moulder by seizing the opportunity to acquire a used, fully overhauled system from KHS. Including all air conveyors, discharge to the packaging and palletising section and an Innocheck FHC fill height control system, the investment came to about €3.5 million.
“With our new line we’ve been able to greatly boost our efficiency — on the one hand thanks to the much higher capacity than on the old line and on the other through a reduction in downtime and larger production series,” said a very happy Tomanović.
Phone: 03 9335 1211
SIG recycle-ready, bag-in-box packaging for wine
SIG has partnered with Australian wine producers to produce a recycle-ready bag-in-box for wine.
BMT Blowscan and Thermoscan rPET bottle perfecting systems
Blowscan and Thermoscan are designed to help manufacturers improve PET bottle performance, reduce...
Henkel Loctite Liofol LA 7837/LA 6265 solvent-free adhesive system for packaging
The system is tailored for applications involving high thermal stresses — in particular...