Improving supply chain sustainability with specialty adhesives for pallet stabilisation
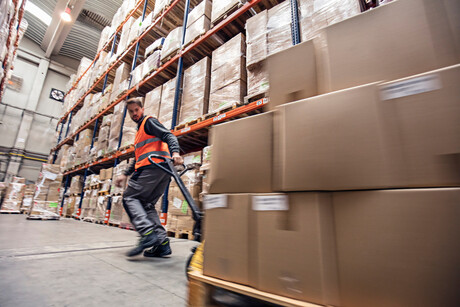
For many years plastic materials have seen widespread use in packaging and logistics, one common application being the use of low-density polyethylene (LDPE) shrink wrap to provide load stabilisation for shipping pallets. But today, environmental sustainability is a prominent topic affecting industry and society overall, with the elimination of single-use plastics a major goal in all aspects of the supply chain.
While reducing the overall use of plastics in consumer goods packaging is an ongoing and product-dependent endeavour, in the area of pallet stabilisation much more can be done right now through the use of hot-melt adhesives.
Traditionally, products packed into cartons are stacked on a pallet for shipment, and in order to prevent the stack of cartons from becoming unstable, the loaded pallet is wrapped in stretch-wrap plastic — often several layers. While the stretch-wrap effectively holds the stack of cartons together, there are cost and environmental pitfalls in using such a solution:
- For large manufacturers there is a significant investment in pallet wrapping machines, whether in-line or robotic, and an ongoing material cost in plastic wrap, as well as maintenance.
- At supply chain distribution centres, pallets can be depalletised by removing and disposing of the stretch-wrap, only to be repalletised, requiring more stretch-wrap to secure the pallet for transportation.
- When pallets are received, the receiving party must remove the wrap and dispose of it, which is labour, cost and space intensive.
- The wrap itself is a single-use plastic and is now recognised as a significant environmental pollutant. Estimates of the natural breakdown time of LDPE in the environment vary from 20 to more than 100 years.
Replacing stretch wrap with palletising adhesives
Hot-melt palletising adhesives can play a major role in helping to reduce the use of single-use plastic wrap, as they offer an increase in safety, sustainability and efficiency along the entire value chain with regards to palletising.
They can significantly reduce — or even fully replace — the need for film and pallet stretch wrap, and by doing so, enable manufacturers, logistics companies, distributors and retailers to meet ever tougher sustainability goals.
Henkel’s Technomelt Supra 7220 PS solution allows the palletising of various items to be performed with minimal or no plastic film, and is suitable for all kinds of filled goods. A hot-melt adhesive joins the outer packages with each other via an automated process, safely securing the pallet. At the receiving end, the items can be removed from the stack without significant force and without damage to the packaging material or carton itself, allowing for fully automated depalletising.
At distribution centres where pallets can be broken down, sorted and restacked, Technomelt Supra 7220 PS also provides excellent pallet stabilisation during transportation when restacking and repalletising is required.
Tests of hot-melt palletising solutions around the world, using Henkel’s Technomelt Supra adhesive, have shown a 90% reduction in shrink film consumption and a reduction in material costs of up to 80%.
Case Studies
Henkel recently participated in trials of its hot-melt adhesive for palletising solutions for two leading beverage producers in South Korea. South Korea has introduced regulations banning the use in the food and beverage industry of plastic materials that are difficult to recycle. This has caused leading beverage manufacturers in the country to introduce 100% eco-friendly carton packaging.
Round-trip pallet slippage test
The first beverage producer was previously using nine layers of non-recyclable film to wrap its pallets. Not only was the film not eco-friendly, but the wrapping time, and time lost when rolls needed to be changed, had an impact on productivity. The anti-slip mats and shrink wrap film were also costly.
The aim was to compare wrapped canned beverages in PE-wrapped trays of 24 355-ml cans, stacked seven layers high against Henkel’s Supra 7320-21 PS hot melt adhesive to hold the trays with high adhesion. Pallets were shipped over a 160 km return journey with:
- Some pallets shrink-wrapped with nine layers.
- Some pallets with hot-melt adhesive and no shrink wrap.
- Some pallets with neither hot-melt nor shrink wrap.
Naturally the non-glued, non-wrapped pallets showed slippage of over 11 cm. The shrink-wrapped pallets showed slippage of 1–2 cm, while those pallets stacked with the Henkel adhesive suffered no slippage at all. When the glued beverage trays were separated there was no evidence of tearing.
The company further analysed the cost savings in using a hot-melt glue solution as compared with stretch film. They found that:
- Stretch film costs four times the cost of hot-melt glue per pallet.
- Manhours were reduced in the palletising process.
- Maintenance costs were significantly reduced.
For the company’s four beverage lines, shipping 576,000 pallets per year, the estimated cost saving was over 63%.
Cardboard carton test
A global beverage manufacturer utilising hot-melt adhesives in their palletising system at their Korean plant performed a trial comparing the Henkel Supra 7220-21 PS adhesive with that of a competitor. The company performed the following tests with cardboard cartons of energy drinks:
- Tilt test: Comparing the degree of tilt and collapse resistance of the pallet during transportation by forklift and truck.
- Tear test: Comparing the appearance of the corrugated cardboard boxes after they have been separated from the pallet on delivery.
- In this case, the corrugated cardboard boxes each contained 12 1.5-litre bottles. The company found that:
- While the competitor’s glue allowed boxes to slip if tilted at 20 degrees, the cartons stacked with the Henkel adhesive maintained stability when tilted up to 30 degrees.
- On receipt of the pallets after shipping for 600 km, those cartons stacked with the competitor’s adhesive showed noticeable cardboard fibre tear when depalletised, while those stacked with the Henkel adhesive remained intact.
Conclusion
By reducing the amount of packaging material, hot-melt adhesive systems are significantly more sustainable and efficient for transporting goods on pallets. As well as reducing the expense of plastic film, and the associated labour and maintenance, the solution removes the additional costs and environmental impact of disposing of materials.
“As a leader in adhesive technologies, Henkel understands how the type of adhesives and coatings used in packaging can have a major impact on recycling and product life extension,” said Daniel Rudolph, President, Henkel Australia and New Zealand. “We are committed to setting new sustainability standards in our Packaging and Consumer Goods business with a holistic approach to sustainability, by creating innovative products and processes through close cooperation with our customers and suppliers.”
Companies globally that are replacing stretch-wrap palletising with hot-melt adhesive systems can confidently say that in the area of logistics, they are making significant improvements in environmental sustainability, while at the same time reducing costs.
Learn more: http://www.henkel-adhesives.com
New Report Reveals Next-Gen Tech Driving Major Growth in Australian Food Processing
With the rise of AI-powered forecasting and automation, the timing is ripe for businesses to...
Racking Up Results: How Jimba Lamb Got Its Inventory in Shape
How a homegrown inventory solution helped United Meat Co's Australian arm, Jimba Lamb, gain...
PE20 Palletising System by Optima Robotics
Amid labour shortages, increasing expenses, and safety worries, businesses of all sizes are...