PepsiCo builds high-capacity logistics automation system in Thailand
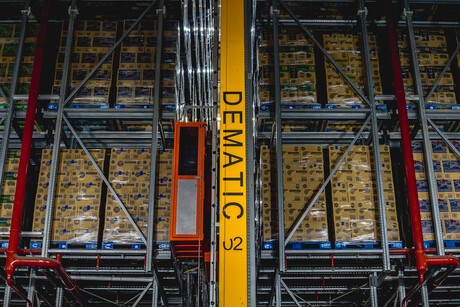
PepsiCo has partnered with Dematic to integrate automation as a central feature of its expanded production and logistics facility in Rojana, Thailand.
PepsiCo’s Rojana facility produces a variety of products. With a growing demand for its products in Thailand, PepsiCo recognised the necessity to build capacity in both production and logistics.
“Rojana is one of our biggest plants, and it also has several different product platforms. We have potato chips, we have Stax-brand chips and we have Fry Pack in extruded products as well. Those products are made at Rojana and are not only distributed nationally across Thailand, but also internationally to Vietnam and other neighbouring countries.” Colin Matthews, Supply Chain Senior Director – IndoChina Foods, PepsiCo, said.
To support PepsiCo’s growth and address space constraints and labour challenges, Dematic worked closely with PepsiCo to develop an automation solution to address its storage, throughput capacity and productivity needs in its logistics operations. The solution centres around an automated storage and retrieval system (AS/RS) with a direct link to both the production and order fulfilment areas.
The AS/RS stores pallets within five aisles of double-deep, high-bay racking with a total of 16,520 pallet locations. A network of pallet conveyors and rail-guided vehicles (RGVs) receives pallets automatically at the end of the production lines and transports them for storage, then directs them from storage to despatch docks or to automatically replenished pick locations for full-case order picking. The solution includes Dematic Warehouse Control System (WCS) software to manage all the automation, the material flow and the inventory as well as to provide real-time tracking and visibility of all transactions.
“The AS/RS is at the heart of PepsiCo’s strategy to enhance its production and logistics efficiency at the Rojana facility,” said Phamondate Rukdee, Sales Manager, Dematic Thailand. “It provides an extremely space-efficient way to store products between when they are manufactured and when they need to be assembled and despatched for delivery to customers.”
The Dematic AS/RS provides fully automated, high-density, high-throughput storage for pallets. It provides complete and real-time visibility of overall inventory, delivering the highest level of accuracy so stock cannot be lost or forgotten. With minimum manual handling needed, product damage and the associated cost and waste are also significantly reduced.
“Previously we had a very manual solution that took a lot of time for people to go around and understand exactly what products we had in the warehouse. In contrast, the Dematic solution is very intuitive. It enables our team to look across the whole of the AS/RS and understand exactly where we have the stock, and they can intuitively and quickly make any adjustments they need to. The AS/RS has more than doubled our capacity and the automation takes us away from the very manual operation we had before. This allows us to supply goods to customers with greater efficiency, leaving them very satisfied,” Matthews explained.
Beyond the benefits described above, the Dematic AS/RS solution also improves warehouse operator safety by dramatically reducing the amount of forklift trucks and other materials handling equipment such as pallet movers, which in turn has reduced accidents, damage and injuries to people and equipment.
The Dematic solution is designed with the future in mind and can be expanded to accommodate additional growth and adapted to changing business requirements.
To learn more about automation within PepsiCo’s Rojana facility, visit dematic.com to view a video case study and to explore the technologies used in this project.
Phone: 02 9486 5555
Loma Flex Conveyor System
Loma Systems demonstrated its latest detection solutions at Anuga FoodTec in Germany.
Flexicon Twin Tilt-Down flexible screw conveyor on mobile base built to 3-A standard
New from Flexicon is a Twin Tilt-Down Flexible Screw Conveyor system with dual hoppers on a...
NORD LogiDrive Advanced and LogiDrive Basic drive solutions
The NORD LogiDrive solution is an energy-efficient, service-friendly and standardised...