Machinery boosts apple processing output
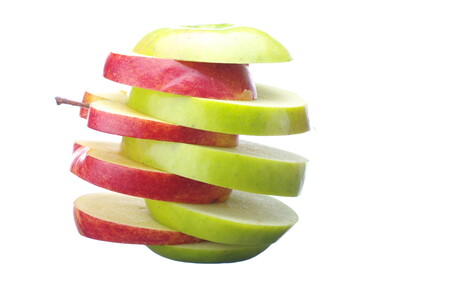
A German apple processing company is benefiting from an increase in processing capacity and an increased level of product safety due to the integration of KRONEN equipment. The company wanted to utilise the equipment that it already had in place in addition to new machinery developed by KRONEN; in doing so it was able to process up to 3000 kg of apples per hour into cubes or segments.
The customer and KRONEN worked together prior to the development of the new line in order to ensure that the old and new machines worked well together, technical compatibility was ensured and that central line control was possible. As the customer had limited space available to them and their current machines would need to remain as is, space considerations were paramount.
The apple processing line developed consists of five apple peelers that move the apples to a dual-belted conveyor belt — the upper belt transferring the usable product and the lower one conveying the waste. A connected inspection belt, equipped with a vibration unit and rinsing shower, allows for the inspection of the apples by five workers.
The line includes a cutting machine as well as a KDB dipping bath, specifically developed for the customer’s needs, in which the apples are dipped thus allowing for increased shelf life and quality. The dwell time in the dipping bath is controlled by adjustment of the belt speed, as the customer had placed importance on specific dwell times and the measuring and dosing system continuously control the ratio of water and washing additive in the dipping bath. The dipping bath was required to be efficient and as such it uses a low amount of water and washing additive.
The line saw ergonomic optimisations too, with production workers being able to work in an ergonomic environment where the height of the different apparatuses was considered in their heights.
Alfa Laval Hygienic WideGap heat exchanger
Alfa Laval Hygienic WideGap heat exchanger is designed to help cut emissions.
SMC VBA air booster regulator and Air Management System (AMS)
SMC develops two energy-efficient solutions for the food and beverage industries.
Kemppi Minarc T 223 ACDC GM all-in-one weld and clean machine
Kemppi has launched an all-in-one weld and clean machine.