Licorice sweets maker installs metal detector for quality check
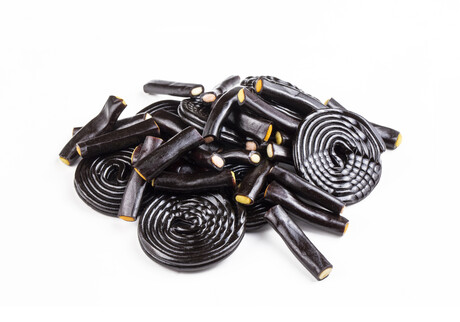
An Italian licorice manufacturer wanted to add a metal detector to its existing production system. The inspection solution was required to identify different kinds of foreign objects, without taking up much space.
For 80 years, Italian food company SAILA (which stands for Italian Liquorice Corporation of Abruzzo — Società Anonima Italiana Liquirizia Abruzzese) has been producing sweets at its historic factory in Silvi Marina, Teramo. The province has a long-held love for licorice which SAILA has been making using a process first adopted by Dominican monks back in the 16th century, but now on an industrial scale. The manufacturer introduced mint-based sweets on its production lines in 1950, which were sold in traditional bags from 1964 and then boxed sweets were launched in 1978.
In order to ensure high-quality standards in the earliest production stages, SAILA decided to use a metal detector to identify the tiniest metal contaminants immediately after the compressor stage, and well before the final packaging of the product.
Minebea Intec created a solution for inspecting the loose sweets using a compact Metalldetektor Vistus/C metal detector that was easy to install in a production line. After the compressor stage, the loose sweets are passed through the metal detector, which has a very small opening for detecting the smallest contaminants. The system is designed to be easy to clean and any products contaminated by a foreign object are identified.
Minebea Intec also provided other control and inspection solutions along the entire production line at the factory. Several checkweigher CoSynus combined model groups (checkweigher and metal detector) were installed in the factory for checking the packaging and ensuring that pre-packaged products conform with Italian Law 690. These weighing machines are then connected to the SPC@Enterprise software, which enables real-time production checks, minimising downtime and improving production performance.
The adopted solution has enabled checks and secure detection of metal contaminants inside the sweets.
In addition, a final check is also carried out using an Essentus checkweigher, which is designed to ensure that no package leaves the factory with a box of sweets missing.
“Our mission is to monitor the entire production line — from manufacture to delivery — in order to guarantee quality at each step,” said Vincenzo Fusco, Director of the SAILA factory.
“Minebea Intec helped us achieve our objectives right down to the smallest detail.”
Phone: 1300 669 162
Wedholms DFC 953 milk cooling tank
The DFC 953 range of milk cooling tanks, which is compatible with revised F-Gas Regulation, has...
Marel Revo FiberFlex patty shaping and processing
Marel's Revo FiberFlex is a burger patty forming and processing system.
ifm Hygienic Flow Meter with IO-Link
The ifm Hygienic Flow Meter with IO-Link is an example of technology in the food industry that...