Minimising Production Waste in Packaging Seal Integrity Testing
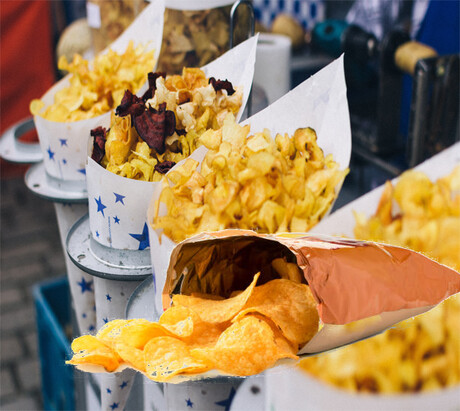
Bestech Australia has supplied the Sealtick TSE6086b flexible packaging leak testers to check the seal integrity of packaging in the production line. Whether food or medical products, quality managers who look to test for packaging leaks can benefit from using Sealtick TSE6086b as it utilizes a non-destructive vacuum decay testing principle. Comparing it with the traditional underwater leak tester, they can determine whether the packages leak without damaging them, which means the products can be returned to the packing line. This creates significant cost savings and minimizes production waste, mainly if the packaging contains high-value and perishable products.
The practice of checking for packaging seals of perishable products has been widely implemented to ensure that external contamination agents do not leak into the packaging. Hence, the products stay fresh for longer. Examples of contaminants can range from air, oxygen, moisture, bacteria, soil and many others.
When oxygen and moisture come in contact with the food products, they act as catalysts to speed up their decomposition by promoting the growth of mold and aerobic bacteria. This is why modified atmospheric gas such as nitrogen or carbon dioxide is added to the packaging to improve their shelf-life and maintain their freshness.
Nowadays, most consumers check for the physical appearance of the packages before buying them from the supermarket. However, microleakages, the primary indicator of food spoilage, are not easily detected visually. Therefore, when the damaged products make their way to the consumer, there is a higher likelihood that the products’ quality has deteriorated and is unsafe for consumption, even if they haven’t passed the stated expiry date.
Technologies for Testing Packaging Leaks
Underwater Leak Testing
Traditional underwater leak testing involves submerging the packages underwater in a pressured, closed chamber. Leaks are detected by looking for bubbles arising from the suspected leak location. This technique primarily relies on the operator to manually observe for leaks.
Pressure decay leak testing
With the vacuum decay leak tester, the packages are inserted in a sealed chamber, which will be put under a controlled vacuum. Packaging leaks can be identified if the chamber takes longer or never reaches the preset vacuum level. It can also detect finer-size leaks, shown by the rapid pressure decay towards atmospheric pressure after vacuum stabilization is turned off. Operators can also program the test method to set the passing standard depending on the package types and the maximum allowable leak rate. The test results are more reliable as leak quantification is independent of operators.
Optical Laser-Based detection system
The laser-based detection system is comparably a new technology that allows manufacturers to test almost all MAP-based packaging in the production line to achieve 100% quality testing, particularly for MAP-based packaging that uses CO2. The system emits a laser beam with a narrow wavelength range in the infrared band to the detector. Leaks are quantified when CO2 gases absorb the specific wavelength in the emitted beam. The presence of CO2 in the test chamber indicates a leak if the packaging uses CO2 as a filling gas.
Quality control and seal testing in the packaging line
Hundreds of thousands of items are processed through each packing line every minute in the manufacturing environment. Manufacturers that wish to implement leak testing as part of their regular quality control must decide which package leak testing systems are suitable for their production line.
Suppose the manufacturers look to achieve 100% testing of products. In that case, the laser-based detection system will be suitable as it can provide automated, fast, accurate leak testing without slowing down the production line. However, this practice may be initially costly if the factory operates multiple production lines. It is also limited as it only targets applications where CO2-filled MAP-based packaging is used.
Identifying leaks through bubbles has the distinct advantage of telling the operators the exact location of leaks. The leak location allows them to identify and fix the problematic machines immediately. However, underwater leak testing is labor-intensive and unreliable, as operators are likely to miss the leaks due to fatigue after long hours of operation. The packages are also damaged as they are wetted and pressurized during the test. Therefore, they must be discarded as production waste, which adds to operational costs.
The vacuum decay leak tester provides an ideal balance between the fully-automated and traditional underwater leak testing. Each test will only take between 5–20 seconds. While manufacturers cannot perform 100% testing with this machine, they can still achieve the main objective by sampling enough packages. Operators can install more machines in the production line if they need to conduct more tests. Furthermore, as the test is non-destructive, the tested packages can be returned to the packing line, preventing waste.
Types of Packaging for Testing
The Sealtick TSE6086b non-destructive vacuum decay packaging leak testers have been successfully used for leak testing applications in the food industry. Examples include manufacturers of milk powders, coffee beans, ready-to-eat salad packs, canned foods, pet foods and dried snacks such as biscuits, chips, etc.
The Sealtick vacuum decay leak testers are suitable for testing in almost all packaging leak testing applications as long as the packages contain gases. As leakages are quantified by the rate of pressure decay, the test is independent of the types of gaseous agents used to fill the packages. Therefore, it provides limitless possibilities for applications not only in food manufacturing industries but also in other industries such as process, medical or pharmaceutical.
The machines are also available in various models and configurations to test the seal integrity of cans and heavy bags. For can leak testers, the sample will be inserted into the custom-designed annulus rather than flexible bags. This configuration is intended to minimize the air volume in the chamber to achieve better accuracy reading.
Consumer packaging comes in a wide range of shapes, properties and configurations. Each type of packaging requires a specific test method for accurate measurement of leaks. With the Sealtick systems, you will have the limitation in testing wet products or products containing moisture. The moisture bubbles may mask the leak during the testing procedure, which provides false and inaccurate results. It is also not capable of testing vacuum-packed products commonly found in cured/processed meats or cheese due to the absence of air.
Industrial Capability
With the robust, stainless-steel housing, the Sealtick system offers long-lasting capability even when used in the industrial environment. All test results are stored in the device’s internal memory for 30 days, which can be easily exported via USB/Ethernet for analysis and quality traceability.
Although the TSE6086b can reliably detect packaging leaks without slowing production, it cannot let the operator know the exact leak location if the package leaks. Generally, the leaking packages indicate problems with machinery at any stage of the production chain. These issues must be immediately addressed to prevent more leaking packages, which may ultimately stop production altogether. Knowing where it leaks will give operators a headstart in identifying the problematic machinery and allow them to make the necessary adjustment without interfering with other processes.
Having an underwater leak tester in the production environment can benefit this case. Operators can plunge the failed packages into this machine to check for the leak location. The bubble leak tester is used as a secondary system to assist operators in finding where it leaks rather than being used as a primary device for packaging quality control.
Local Technical Expertise and Support
Quick access to local technical support is crucial in B2B and manufacturing industries, as extended downtime due to system failure is costly to the organization. Our engineers at Bestech Australia have developed the Sealtick leak testing system and manufactured them in-house. With our extensive knowledge and experience, we can assist you with all your packaging leak testing requirements.
For more information, visit www.bestech.com.au
Boxes on demand: machine revolutionises packaging practices
No more time wasted making boxes and no more issues with box warehouse logistics, the Boxway...
Revolutionizing Packaging Efficiency: Henkelman's Automatic Solutions
Henkelman Australia, a leading force in the industry, is reshaping the Australian packaging...
More than you expect. Packaging. Sensors. Solutions.
Automated systems for production and packaging processes need to be more flexible, more...