Insourcing PET bottle production pays off
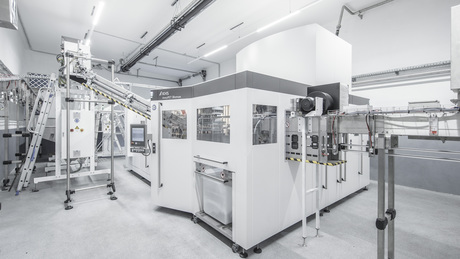
The management at German mineral water bottler Herzog Mineralbrunnen had long been toying with the idea of producing PET bottles on-site rather than buying them in ready-made. However, there was concern that there was not enough room for the new system, the effort involved in converting the engineering seemed too great and the existing production set-up was established and running well.
Then, in 2014, plant manager Gerd Stork attended a trade show and met Frank Fretwurst, head of Area Product Management for KHS Corpoplast. At the end of their conversation, Fretwurst was convinced that the Herzog bottling plant held potential for making savings. He suggested the company consider a KHS InnoPET Blomax Series IV stretch blow moulder. Herzog Mineralbrunnen would buy in PET preforms, which are much cheaper than finished bottles, and these would be manufactured on-site.
The machine has low operating costs; however, the site in Bochum did not have the necessary electrical power, meaning that new cables had to be laid and the transformer house expanded. The new system would also need an extension connected to the existing filling section by conveying segments. However, the company considered that the potential savings were worth the effort.
Moving towards greater efficiency
In total, Herzog Mineralbrunnen invested around €1.6 million in the new engineering set-up. The system has been operational since August. The KHS InnoPET Blomax Series IV stretch blow moulder has a capacity of up to 13,500 bottles per hour, which gives the medium-sized family business a capacity utilisation of around 80%.
The energy efficiency and compact design of the machine were major criteria in Herzog Mineralbrunnen’s decision to invest, as well as the quality of the bottles, which continue to have optimum stability and low weight.
“It’s important that production doesn’t stop. All of our lines run continuously,” states Stork. Approximately 35% of all products leave the production line in PET, with the rest in glass. “The percentage of PET is growing, however,” he says. The plant in Bochum fills about 29 to 30 million PET bottles a year.
To meet the varying demands of the company’s production operations, the heater on the KHS InnoPET Blomax Series IV can be used in combination with any type of transfer and blow moulding equipment. Because the heater is modular, upgrades such as additional heating chambers can be installed at a later date. The stretch blow moulder can also be adapted to cater for any extensions to the product portfolio whenever needed.
“In two years, the system will have paid off. We have more line availability and are more flexible,” says Stork.
Phone: 03 9335 1211
Parkside Recoflex recyclable paper-based packaging
Parkside's Recoflex is a range of recyclable, paper-based, flexible packaging materials.
Innovia Films RayoFloat white APO (WAPO) floatable shrink sleeves
Innovia Films launches white floatable PO shrink film for light-sensitive products.
Parkside Popflex lidding film
The Parkside Popflex lidding film provides a recyclable solution for fresh produce packers and...